From Field to Foundation: How Bio-Based Materials Are Growing the Future of Housing
In a quiet field somewhere in North Dakota, rows of tall, leafy hemp plants sway in the wind. A few states away, in Georgia, acres of bamboo stretch to the sky. And in countless corners of the world, crops once used for textiles, food, or insulation are now being reimagined as walls, roofs, and even entire homes.
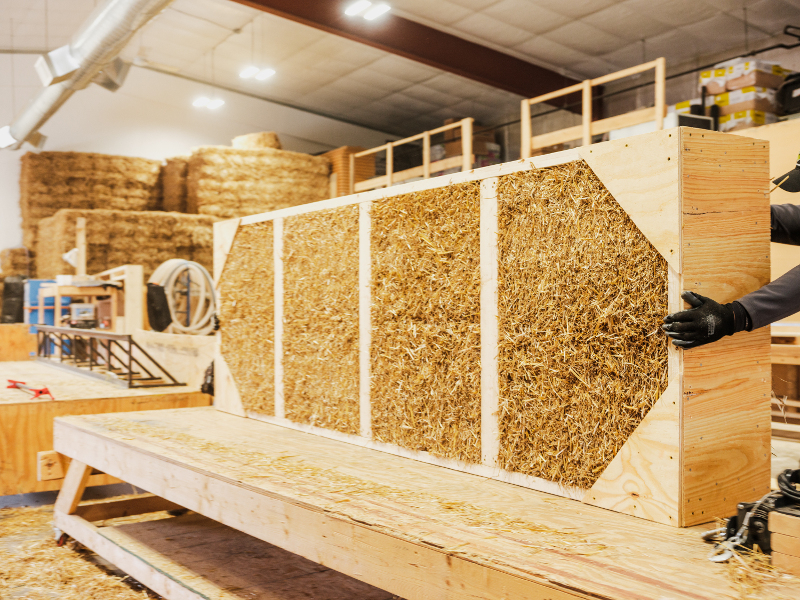
Welcome to the world of bio-based building materials—a movement where the future of housing starts in the soil and ends in a structure. For modular and offsite construction innovators, the journey from field to foundation isn’t just about sustainability. It’s about opportunity.
Let’s dig into how these materials are grown, processed, and now woven into the very framework of tomorrow’s buildings—and why offsite construction might be the best place for this revolution to take root.
The Roots of Change: Where It All Begins
The term “bio-based” refers to materials derived from living or once-living organisms—typically plants. These include hempcrete, bamboo panels, flax-based insulation, straw bales, and mycelium bricks (yes, mushrooms). Unlike traditional materials that require mining, smelting, or high-carbon production processes, bio-based products often regenerate yearly, absorb CO₂ during growth, and can break down harmlessly at end of life.
But these aren’t backyard garden materials—they’re becoming serious contenders for structural and thermal performance. Hempcrete, for example, offers excellent insulation and vapor permeability while being fire-resistant and carbon-negative. Bamboo is stronger than steel in tension and can be processed into sleek laminated panels rivaling engineered wood.

As demand grows for homes that are healthier to live in and lighter on the planet, the raw materials are literally sprouting beneath our feet.
Harvesting the Potential
One reason bio-based materials are catching on now is timing. Climate anxiety is high. Government incentives are shifting. Builders are seeking greener materials that don’t cost double. And modular construction is poised to take full advantage.
Why? Because offsite builders operate in controlled environments where new materials can be tested, refined, and scaled. You’re not battling weather delays or inconsistent labor on-site. You can prototype a wall panel made from hemp-lime composite on Monday and tweak the process by Wednesday. That’s a level of agility that site-built contractors can only dream of.
Factories that partner directly with growers or regional suppliers also stand to benefit from material consistency and price stability. As global supply chains wobble, building local may not just be eco-friendly—it might be necessary.
From Field to Factory: A Modular Match
Let’s say you’re building a small-footprint modular home with high thermal requirements and an eco-conscious client base. Traditionally, you might use fiberglass insulation and standard gypsum board. But imagine this:
- Walls framed with laminated bamboo
- Insulated with flax or straw panels
- Sealed with lime plaster
- Wrapped in mycelium board for breathability and fire resistance
Every one of those materials is plant-based, and every one of them can be pre-assembled in an offsite production facility. The result? A modular home with significantly lower embodied carbon, better indoor air quality, and a compelling story that resonates with next-gen buyers.
That’s not fiction. That’s what a growing number of European factories—and a few bold U.S. operations—are doing right now.
Barriers Still Sprouting
Of course, not everything’s rosy in the bio-based world. There are real challenges that make some factory owners raise an eyebrow:
- Code compliance: Many building officials still don’t know what to do with hempcrete or straw walls. Testing and certifications lag behind.
- Supply chain limitations: Consistent sources of plant-based materials aren’t available nationwide. This makes regional adoption more feasible than national rollout (for now).
- Processing complexity: Turning raw plant material into construction-grade components isn’t easy. It requires drying, treatment, forming, and quality control that not all startups are ready to handle.
But none of those are deal-breakers. They’re infrastructure problems, not product problems. And infrastructure can be built.
What’s in It for Offsite?
Offsite construction has always been about optimization—doing more with less, faster, cleaner, and more consistently. Bio-based materials offer the same logic: more performance from less input, faster renewability, cleaner lifecycle, and consistent thermal or structural behavior once scaled.
They also offer a marketing advantage. People want to live in homes that feel like they belong to the earth, not ones built like a machine. If a modular factory can tell a client, “This home was grown before it was built,” that’s a story that sticks.
We’re entering a time where materials need to do more than just meet spec sheets. They have to meet expectations, values, and climate goals. And if you’re in offsite construction, you’re already ahead of the curve. Why not stay ahead by planting something new?
Green Shoots of Promise
The rise of bio-based building isn’t a flash in the pan—it’s a seedling industry, still growing but deeply rooted in both innovation and common sense. As more offsite factories explore ways to differentiate themselves, solve climate challenges, and meet shifting market demands, the field-to-foundation model is going to bloom.
So the next time someone tells you modular homes are just “boxes,” you can smile and say, “Yes—and some of us grow the box before we build it.”
Want to see which plant-based building startups are making waves in offsite? Stay tuned for our next piece where we spotlight 5 innovators quietly changing the way homes are grown.
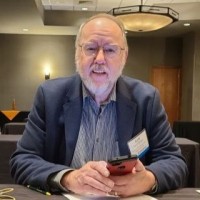
Gary Fleisher
Gary Fleisher is the Leading Observer of the Offsite Housing Construction Industries. He has been actively involved in researching and writing about the latest trends and developments in the industry for over a decade now.
With his extensive knowledge and experience, Gary has emerged as a go-to expert for businesses looking to stay ahead of the curve in the modular construction industry. In addition to his work as an editor, he is also a sought-after speaker and consultant who has helped numerous companies achieve strategic and operational success.