Built in the factory. Blocked in the permit office.
In modular and manufactured housing, staying compliant with an ever-growing list of codes, standards, and certifications isn’t just important—it’s essential. That’s where third-party inspection agencies like PFS TECO come in, ensuring quality and compliance at every step of the building process.
To gain a deeper understanding of what these inspections entail and how they impact the offsite construction industry, I sat down with Bob Gorleski, a nationally respected expert on building code compliance and inspection protocols.
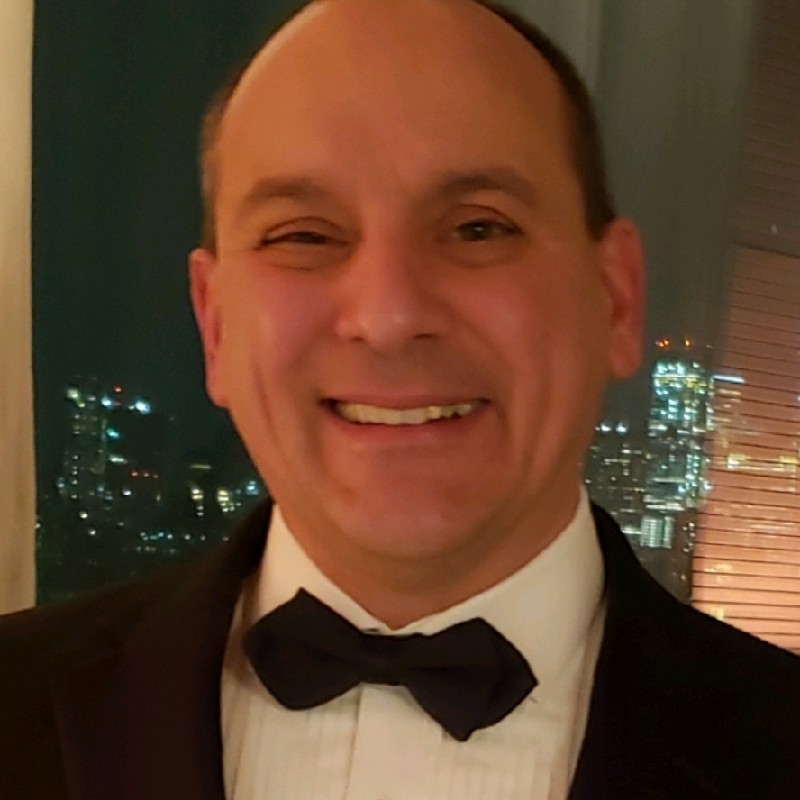
Robert Gorleski
With over 35 years of experience and a résumé that spans nearly every major facet of code enforcement—plan review, QA, field inspections, and engineering—Bob is the guy you want in your corner when navigating the complexities of state, national, and industrialized building regulations. His unique perspective comes not only from his hands-on work, but also from his service with respected organizations such as the Manufactured Housing Institute, the Modular Building Institute, and the Wisconsin Housing Alliance.
Bill Murray, Co-Founder of Offsite Innovators: Would you please explain the role of PFS and third parties in offsite construction and manufacturing?
Bob Gorleski, Vice President of the Manufactured Structures Division at PFS TECO: PFS Corporation d.b.a. PFS TECO is a third-party agency providing independent oversight for off-site construction and manufacturing. Our responsibilities include plan review, quality assurance monitoring, and in-plant inspections to verify that production aligns with approved designs and complies with applicable codes. Since local jurisdictions don’t inspect work performed in a factory setting, PFS TECO ensures that units are built to code before they leave the plant. They manage label control and serve as the point of contact with state or federal regulators. Our role is essential to maintain accountability, ensuring code compliance, and supporting consistent quality in a production-driven environment.
Bill: From your perspective at PFS, how well do current building codes align with the realities of off-site construction?
Bob: From our perspective, current building codes were developed for site-built construction and often don’t translate well to the factory floor. They assume field inspections, on-site sequencing, and installation methods that don’t reflect how off-site construction operates. This creates gaps, forces workarounds, and adds unnecessary steps that disrupt production without improving outcomes. For example, codes often require inspections “before cover,” but in a factory, components like floor framing and mechanical runs are typically enclosed within hours, long before an inspector could review them under a traditional model. While HUD and some state modular programs have adapted portions of the code to fit the factory environment, there’s still a lack of consistency and clarity. We see a clear need for better alignment between code requirements and how work is actually performed in off-site manufacturing.

Bill: What sections of the IRC or IBC present the most common challenges to off-site manufacturers?
Bob: The most common challenges off-site manufacturers face with the IRC and IBC relate to code sections that assume on-site construction processes and inspections. These include structural framing and bracing requirements, fire separation and means of egress, installation and inspection of mechanical, plumbing, and electrical systems, and exterior weatherproofing details. Energy efficiency provisions often don’t fully account for factory-controlled installation methods. Because these codes are written with site-built construction in mind, off-site manufacturers frequently must find alternative compliance paths or rely on engineering approvals to meet the intent of the code without disrupting production.
Bill: In your experience, which tends to be more difficult for offsite construction—state-level codes or local jurisdictional enforcement?
Bob: In our experience, local Authority-Having-Jurisdiction (AHJ) enforcement presents more challenges for off-site construction than state-level codes. State programs are typically standardized and include provisions that recognize factory-built construction and third-party oversight. Local AHJs, however, may not be familiar with off-site processes or the scope of factory inspections, which can lead to inconsistent interpretations, redundant inspections, and added requirements at the job site. This disconnect often results in delays and frustration, despite the unit meeting state-approved design and inspection criteria. Aligning expectations between factory-built systems and local enforcement remains a key hurdle.
Bill: HUD code is often contrasted with modular programs. How do the two compare in terms of flexibility, cost, and permitting ease?
Bob: HUD Code and modular programs differ in key areas. HUD is federally preemptive, streamlining approval and limiting local interference—once labeled, a unit can be shipped and installed in any state without additional plan review. Modular programs follow state-adopted versions of the IRC or IBC, which means added complexity, varying requirements, and local Authority-Having-Jurisdiction involvement. Modular offers more design flexibility, including multi-story and custom layouts, but at a higher cost due to engineering, state reviews, and permitting fees. HUD, while more limited in design, benefits from standardized construction and lower regulatory and production costs.
Bill: Are code officials generally receptive to innovation (off-site), or is there still a mindset that favors traditional site-built construction?
Bob: Most code officials still lean toward traditional site-built construction. While exceptions exist, many remain unfamiliar with off-site processes and are skeptical of third-party inspections and factory-based compliance. As a result, local Authorities Having Jurisdiction often impose redundant inspections or apply site-built assumptions to factory-built units—even when those units have already been approved at the state level. The issue isn’t outright resistance to innovation but a lack of exposure to how off-site construction actually works. That said, the mindset is beginning to shift as more jurisdictions gain experience with modular and HUD Code homes, and as education efforts around offsite methods improve.
Bill: Can you recall a recent example where a code provision or inspector’s interpretation significantly impacted an off-site project?
Bob: A HUD Code home was installed on a permanent foundation in a state that typically sees manufactured homes placed on piers. The local inspector, unfamiliar with HUD’s guidelines for foundation systems, delayed the final inspection, questioning the anchoring method, even though it followed an approved engineered design. The confusion over HUD’s preemptive authority and foundation alternatives led to weeks of delay while documentation was resubmitted and the inspector was educated on the applicable standards.
Bill: Are there any coordinated national efforts or organizations working to make codes more compatible with off-site construction?
Bob: Several national organizations are actively working to improve how building codes address off-site construction. The Modular Building Institute (MBI) advocates modular construction by collaborating with the International Code Council (ICC) and educating code officials to remove unnecessary barriers in plan approvals and inspections. The Manufactured Housing Institute (MHI) represents HUD Code manufacturers. It works with HUD, state agencies, and lawmakers to update federal regulations and ensure local officials do not impose extra requirements that conflict with HUD’s federal authority. The ICC Off-Site and MBI also develop specific standards that reflect factory-built processes rather than traditional site-built assumptions. Together, these organizations are driving changes that better align codes, standards, and enforcement with the unique workflows and efficiencies of off-site construction.
Bill: What role is PFS playing—or could play—in shaping a more modern regulatory framework?
Bob: PFS TECO plays a key role in modernizing the regulatory framework for off-site construction. As an independent third-party inspection agency, we verify that factory-built units comply with code requirements before leaving the plant. This reduces the need for duplicated local inspections and increases AHJ confidence in off-site methods. We actively engage in code development and industry groups, providing practical insights from factory inspections to help shape regulations that align with off-site construction realities. PFS TECO supports streamlined, risk-based enforcement that promotes innovation without compromising safety or quality by connecting manufacturers, regulators, and local inspectors.
Bill: Do you think industry is making progress, or are we at risk of being left behind by overly rigid codes?
Bob: The industry is moving forward, but challenges persist. Awareness and acceptance of offsite construction are improving, driven by groups like MBI, MHI, and third-party agencies like PFS TECO. Still, many codes and local enforcement practices remain rooted in site-built assumptions that don’t fit factory-built methods. If regulatory updates don’t keep pace, offsite construction risks are being held back by codes that stifle innovation and efficiency. Ongoing education, advocacy, and collaboration are critical to maintain progress and prevent being left behind.
Bill: If you could change one aspect of the current code environment to accelerate offsite adoption, what would it be?
Bob: Consistent acceptance of third-party inspections and plan reviews is essential to eliminating redundant inspections and plan reviews, reducing delays, and accelerating off-site construction adoption.
Bill: What can builder developers do to effectively act as catalysts to promote code related changes necessary to accelerate the use of offsite construction?
Bob: Builder-developers can promote code changes by working with industry groups, sharing examples that show off-site construction works, talking directly with code officials, and pushing for rules that fit factory-built methods. Their experience and influence help drive practical updates that support faster, more efficient building.
Throughout our interview, Bob made one thing clear: third-party inspections aren’t a bureaucratic hurdle—they’re a safeguard. They help protect homeowners, support manufacturers, and maintain the integrity of the entire offsite construction industry. His passion for building better, safer, and more inclusive spaces (as seen in his work on modular classroom accessibility) is evident in every project he touches.
We’re grateful to Bob Gorleski for sharing his time, insight, and years of expertise. His commitment to regulatory clarity and code compliance continues to benefit not only the clients of PFS TECO but also the entire modular building community. For further information or questions, Bob can be reached directly at [email protected].