Revolutionizing Passive Cooling in Modular Construction: The Many Benefits of DrainStrip™ – with video
For centuries, builders have relied on natural ventilation to keep buildings cool and dry. Before the era of modern air conditioning, homes featured elevated roofs, ventilated attics, and airflow gaps behind exterior materials to regulate temperature and moisture. These passive cooling techniques not only enhanced comfort but also preserved the longevity of structures.
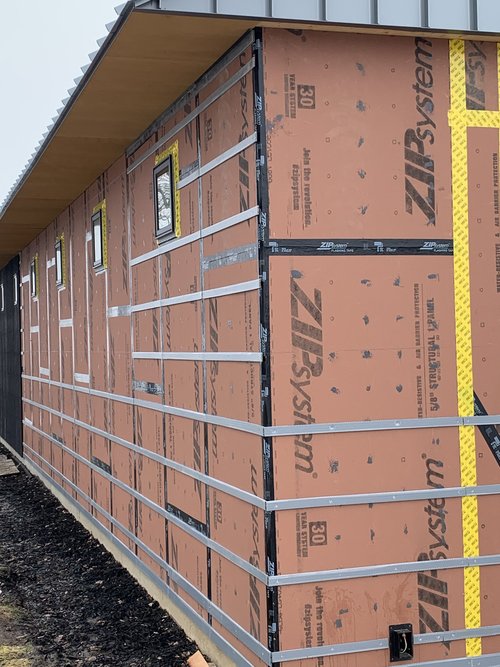
.
However, as modern construction methods evolved, these time-tested solutions were largely abandoned. The result? Buildings that trap heat, accumulate moisture, and suffer from premature material degradation—all while increasing energy costs. But what if there was a way to bring passive cooling back into modern modular and offsite construction?
Enter DrainStrip™, an innovative ventilation and drainage solution that reintegrates these essential building science principles, delivering a simple, cost-effective way to enhance durability and energy efficiency in offsite-built structures.
What is DrainStrip™?
DrainStrip™ is a built-in rainscreen and ventilation system seamlessly integrated into TSUPS™ (Thermal Studs Ultimate Panel System) wall, roof, and floor panels. It introduces a continuous ventilation and drainage gap behind cladding, siding, and roofing materials, preventing moisture buildup and thermal stress.
Another plus is DrainStrip™ can be used in any wall or roof assembly!

.
This groundbreaking approach offers a host of benefits, including:
✔ Enhanced Energy Efficiency – Improves airflow and reduces heat retention, lowering cooling costs.
✔ Moisture Protection – Prevents trapped condensation, eliminating mold, rot, and siding failures.
✔ Material Longevity – Extends the lifespan of exterior finishes by reducing expansion, contraction, and water damage.
How DrainStrip™ Works on Walls
In conventional construction, cladding and siding are directly attached to sheathing, leaving no space for airflow or moisture drainage. This leads to excessive heat buildup, material warping, and trapped moisture—problems that contribute to premature siding failure and structural damage.
By incorporating DrainStrip™ within TSUPS™ panels, a natural ventilation gap is created behind exterior cladding, allowing:
✔ Passive cooling to reduce thermal stress on siding.
✔ A continuous drainage plane to channel moisture away.
✔ Improved air circulation, which dries materials faster and prevents mold growth.
This built-in rainscreen system eliminates the need for additional furring strips or labor-intensive drainage layers, making it a hassle-free solution for both builders and factory-produced modular structures.
How DrainStrip™ Works on Roofs
Heat buildup under roofing materials is one of the biggest contributors to high cooling costs, especially in prefabricated and modular homes. Roofs act like thermal batteries, absorbing and radiating heat into attics and living spaces. Without proper ventilation, various roofing materials suffer:
✔ Steel roofs trap heat, turning attics into ovens.
✔ Cedar shake roofs accumulate moisture, leading to accelerated rot.
✔ Clay tile roofs retain water, causing long-term material degradation.
DrainStrip™ eliminates these problems by creating a breathable air gap between the roofing material and TSUPS™ panels. This passive ventilation system allows hot air to escape, preventing excessive heat transfer into the structure. The result?
✔ Cooler roof surfaces that reduce AC demand.
✔ Efficient moisture drainage, stopping rot and mold before they start.
✔ Extended lifespan for all roofing materials.
A Smarter Way to Build: DrainStrip™ and the Return of Passive Cooling
Historically, homes were designed to breathe. Tall ceilings, shaded porches, ventilated attics, and strategic airflow gaps all worked together to keep homes cool and dry without artificial climate control. As modern construction methods emphasized airtight designs, we inadvertently suffocated our buildings—leading to higher energy consumption and costly material failures.
DrainStrip™ and TSUPS™ panels offer a smarter alternative, reintroducing passive cooling into offsite construction without the added cost of extra materials or labor. By integrating built-in ventilation and drainage, modular builders can deliver:
✔ More durable, energy-efficient homes that require less maintenance.
✔ Reduced heating and cooling loads, cutting down on operational costs.
✔ A more sustainable construction approach that aligns with net-zero and high-performance building standards.
As the offsite industry pushes for innovation, DrainStrip™ presents an opportunity to rethink how we build, embracing both modern technology and timeless building science.
Let’s stop trapping heat and moisture inside our buildings—and start letting them breathe.