an article by David Chiles
If you’ve been in the construction industry for any length of time you know that there is a continued and growing focus on product performance and sustainability. Construction materials have not changed that drastically in the last 50 years. Whether you are a builder or manufacturer you’re likely going to choose between 3 common building materials, Wood, Concrete or Steel.
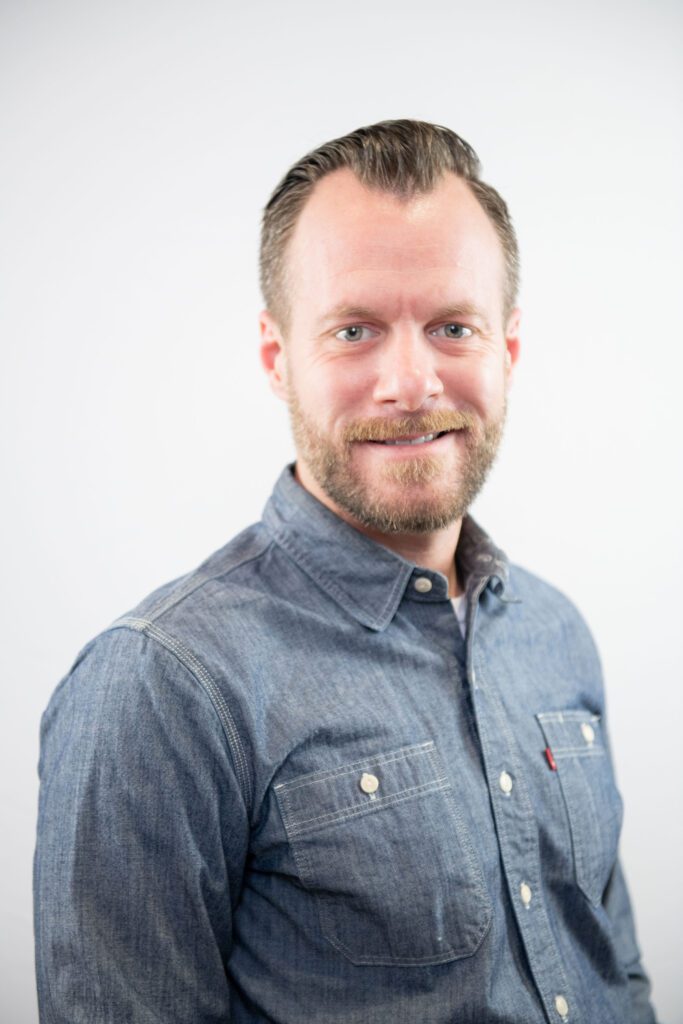
David Chiles
While wood serves as a great balance between efficiency and affordability and concrete excels in strength and versatility. This article will explore some of the attributes of light gauge cold-formed steel framing (LGS/CFS) and its performance features.
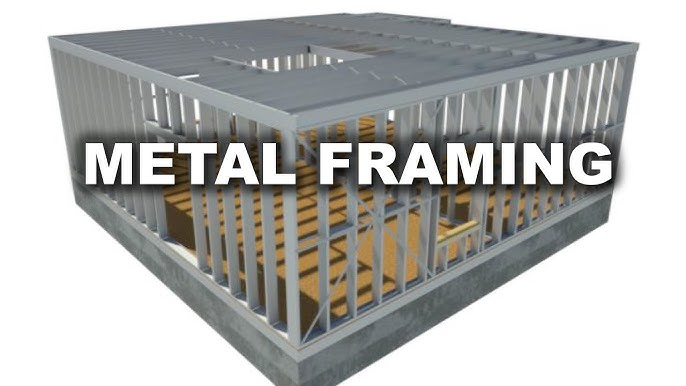
All photos – ClarkDietrich Framing Systems
Sustainability: Reduce, Reuse and Recycle
Cold-formed steel (CFS) framing is a sustainable building solution that embodies the “Reduce, Reuse, Recycle” principles. It’s precise manufacturing minimizes waste, while its lightweight nature reduces transportation emissions. CFS can be easily disassembled and reused in new projects, thanks to its durability and non-combustibility. At the end of its life, CFS is 100% recyclable back into new steel products without quality loss. Choosing CFS reduces construction waste, conserves resources and contributes to a circular economy in the building industry. (AISC, 2024)
Much of the industry started its journey to greater sustainability by incorporating or increasing their products recycled content. However, some materials experience downcycling, a breaking down of material integrity and performance after each recycling iteration. This downcycling can often times affect the structural performance of the original product manufactured from virgin materials. The best example is the case of wood products. Wood framing members can be downcycled into paper products, and those paper products are then downcycle one or maybe two more times before they must go to a landfill.
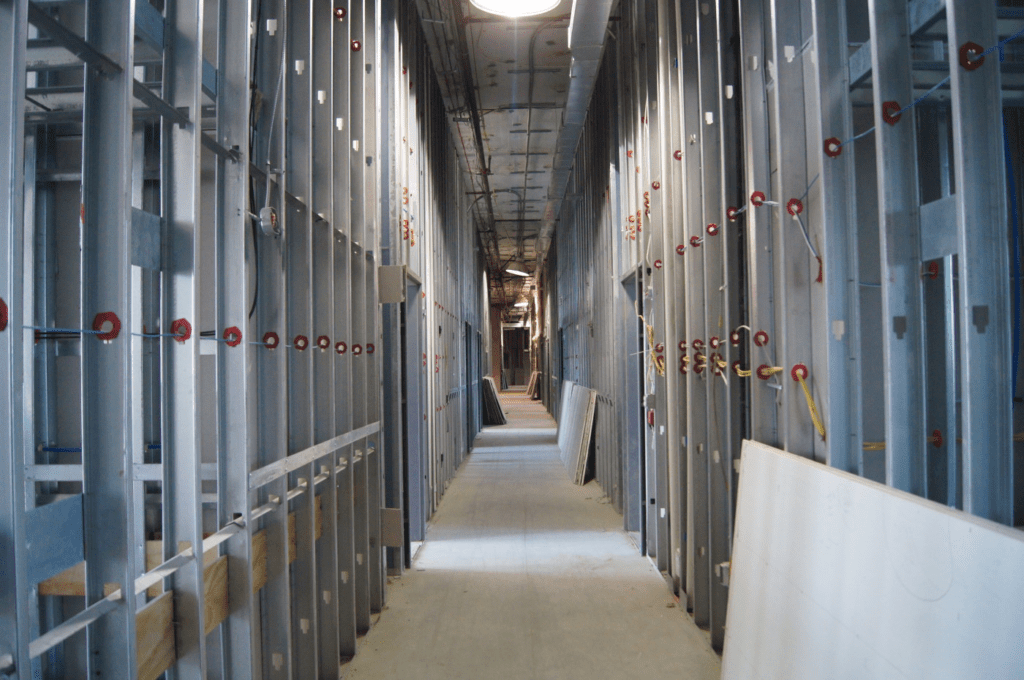
Steel, on the other hand, is infinitely recyclable and does not experience downcycling. In fact, when you buy steel, you are always buying a recycled product. 80 million tons of steel scrap are recycled each year – more than paper, aluminum, glass and plastic combined.
Did you know that the average 2,000sqft home, built with wood, requires 40-50 trees or one acre of deforestation? If you were to construct that same size house out of CFS it would contribute to the recycling of four automobiles.
According to an EPA estimate, 600 million tons of construction and demolition debris were generated in the United States in 2018, (EPA, 2018). Furthermore, recycling one ton of steel scrap saves 1.5 tons of CO2 and almost 2 tons of raw materials. (worldsteel.org 2024)
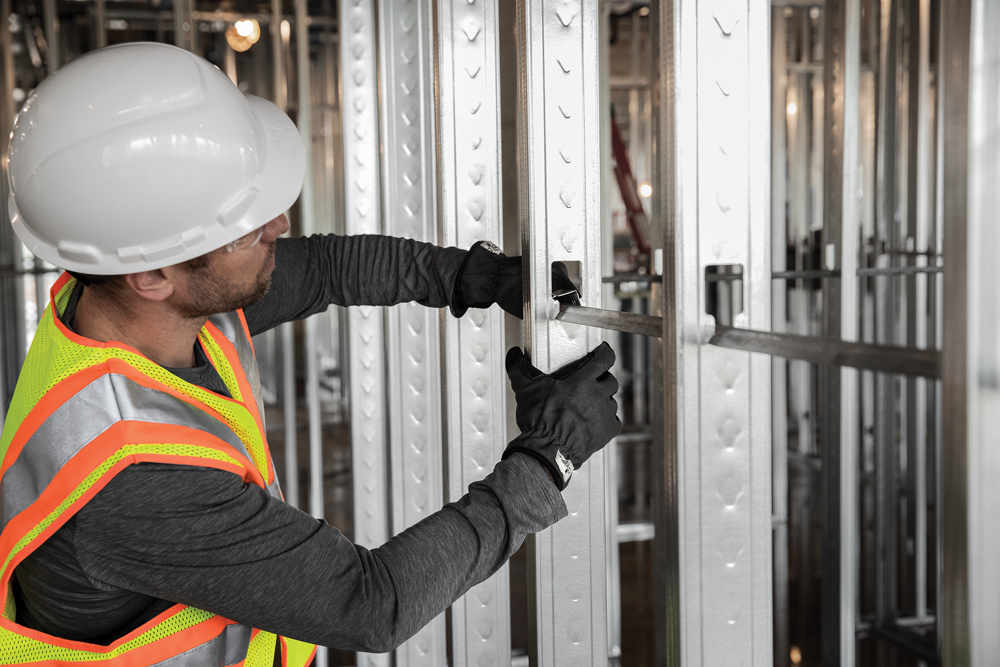
Strength and Versatility
Steel is roughly half the weight to its wood counterparts. A reduction in weight of framing materials helps reduce the requirements for your project’s foundation. If your project incorporates off-site construction practices, then less weight allows for more material to be shipped per truck load and possibly less overall deliveries. Furthermore, the reduced weight of CFS is advantageous for seismic design, where the weight of a completed structure is a crucial consideration.
Steel’s strength also lends itself well to mid-rise construction. The sweet spot is 6-9 stories over a one level podium. An increased project height allows for smaller project footprint and greater efficiency in site development. Small considerations like these, directly contribute to reducing a carbon footprint for a project, while increasing the value of the project long term.
Steel is dimensionally stable and manufactured to exact lengths and tolerances. Because CFS is dimensionally stable, it does not warp, shrink or settle over time. These features lend itself to greater design flexibility in terms of taller wall heights and greater spans.
CFS’s galvanized coatings provide moisture and humidity resistance. The galvanized coatings on sheet steel must meet requirements for ASTM standards to qualify for CFS manufacturing. These ASTM standards test the hardness, malleability, ductility and corrosion resistance of the steel through rigorous testing.
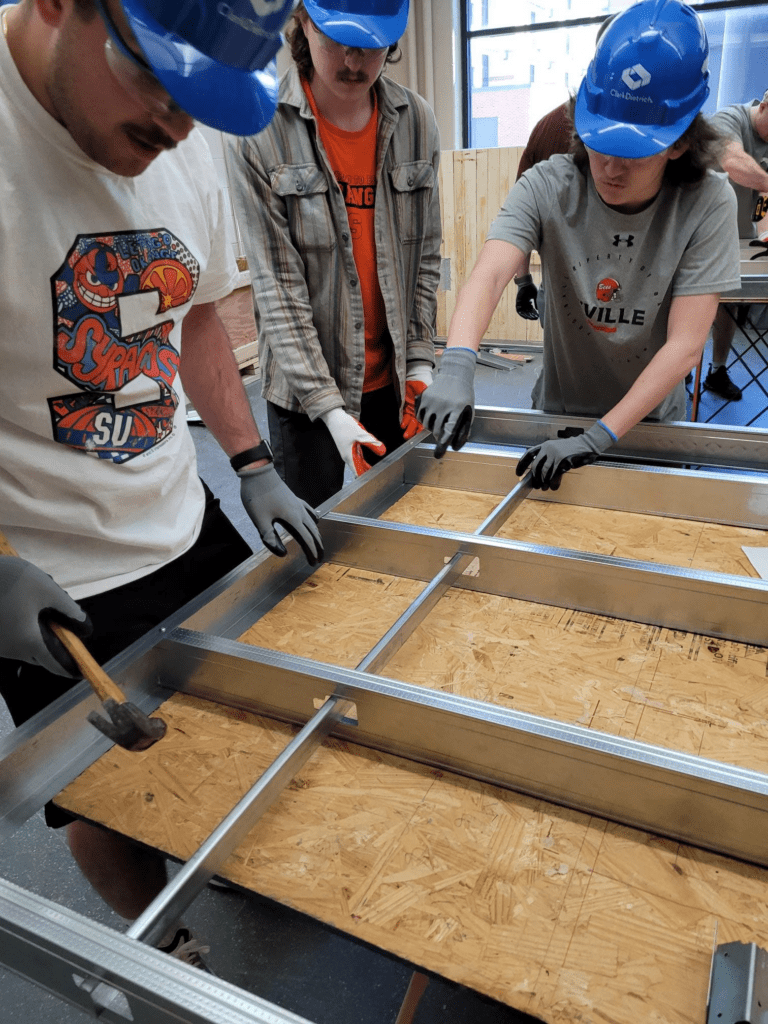
Fire Safety
Possibly the largest concern and deciding factor for any building material we choose to incorporate in a project. In a fire or pre-fire condition, steel framing will never directly fuel or contribute to the spread of the fire. At the risk of stating an obvious point, wood at its core will always be a fuel source for fire. No matter what chemical you soak or treat it with, it will burn, you can slow the burn or char rates, but it will be significantly weakened structurally and pose a greater life safety risk.
Lately, the offsite community has looked at mass timber in an effort to mitigate the shortcomings of traditional wood framing. While mass timber answers the question for mid- and high-rise construction, mass timbers is a resource intensive production process. The possible environmental impact of their adhesives and machinery having the largest footprint to account for.
Non-combustible materials are still the best and safest choice for any construction project be it traditional or off-site construction. Many municipalities across the country have conducted studies of the true cost of combustible frame residential buildings and their assessments often lead to changes in the building code. A fire in a combustible frame project of any kind is a risk unto themselves and surrounding properties. In that scenario, the total losses comprise of the project, surrounding properties, displaced families and exhausted municipal resources.
Affordability
If there is one thing that seems to be on the mind of most participants in our industry, it’s the existing and continued demand for affordable housing. While the task ahead is monumental the demand for affordable housing is a factor that all of us in the industry have a shared goal on impacting.
In some instances, steel framing might be a higher cost on a stick-by-stick comparison to wood framing and concrete is generally more expensive than wood or steel framing combined when you break it down to a square foot price.
Steel framing however offers significant savings in terms of risk and liability and lifetime building operation. Cost studies have revealed that projects constructed in CFS over wood are generally 2-3% higher on a stick for stick basis. Those same studies often reveal that the property insurance premiums and builders risk insurance are substantially less when constructed in CFS(Costs to Build with Cold-Formed Steel Versus a Wood-Framed Building, SFIA 2024)
Cold-Formed Steel is an inorganic non-combustible material, it resists mold and mildew and will never be a food source for pests like termites. These qualities as well as it’s fire resistance properties can reduce insurance premiums as much as 25 to 75 percent. (SFIA 2024)
A final component to CFS’s affordability is how easily the average participant can source steel framing. There are multiple volumetric roll-forming manufacturers and there are multiple brands of roll forming equipment that allow you to have greater control over your manufacturing process’.
Closing Thoughts
During the course of my travels and visits to many off-site participants in the last couple of years, I’ve seen a healthy mix of different framing materials used in many configurations. Sadly, for some participants, they simply choose the building product that they know or have experience with regardless of its features or benefits. I don’t think that any one specific building material is greater than the other, and on any given construction project there is a likely combination of concrete, wood and steel products that make up the whole of the project.
However, knowing what we know as an industry about green building, renewable resources, climate change and decreasing carbon footprint it begs the question, why isn’t steel a leading choice for more project stakeholders. Currently, steel makes up less than 1% of all new residential construction starts. (Eye On Housing 2023)
There is no denying that wood framing has been the primary choice of builders for millennia. But in our modern world and the ever-evolving construction industry, regardless of what product we favor, we can all agree that we need to consider the materials we use. This primary consideration will help guide our industry with a continued focus on the true impact we leave on the built environment and the future of our planet.