The construction industry is experiencing a seismic shift. Stricter energy codes, coupled with rising consumer demand for energy-efficient homes, are redefining the way modular and wall panel factories approach building design and material selection. Amid these challenges, one innovation stands out as a game-changer: ThermalStuds. By combining superior insulation capabilities with structural reliability, ThermalStuds not only meet but exceed modern energy codes with ease, offering factories a competitive edge.
Here’s why your factory should seriously consider integrating this innovative product into your production line.
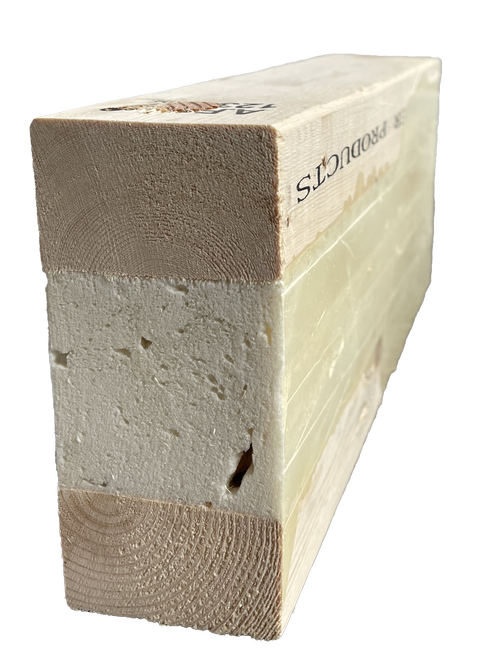
The Challenge: Navigating the Maze of Energy Codes
In recent years, energy codes have become increasingly stringent. Standards like the International Energy Conservation Code (IECC) require higher R-values and reduced thermal bridging, pushing manufacturers to rethink their materials and processes. Non-compliance is not an option—it leads to costly redesigns, delays, and, ultimately, lost business.
For modular and wall panel factories, this means a relentless search for materials that meet energy requirements without compromising structural integrity, speed of assembly, or cost-efficiency. Traditional solutions, such as exterior insulation or double-stud walls, often increase labor and material costs while complicating the production process. This is where ThermalStuds shine.

The Solution: ThermalStuds as a One-Step Answer
ThermalStuds offer a revolutionary approach to framing by integrating thermal breaks into the structure itself. These studs are designed to drastically reduce thermal bridging—the Achilles’ heel of traditional framing systems. By eliminating the direct path for heat to escape, ThermalStuds help walls achieve higher energy efficiency without additional layers of exterior insulation.
Key benefits include:
Increased R-Values: ThermalStuds significantly boost wall insulation performance, helping your products comply with even the toughest energy codes.
Ease of Integration: Designed to fit seamlessly into existing production processes, ThermalStuds require minimal retraining or retooling.
Cost-Effective Compliance: By reducing the need for additional insulation layers, ThermalStuds can lower material costs and speed up assembly times.
Durability and Strength: Made with advanced materials, ThermalStuds deliver the structural integrity required for modular and panelized construction.
Why Modular and Wall Panel Factories Should Act Now
The construction industry is under immense pressure to build better, faster, and more sustainably. Consumers want homes that are energy-efficient, and governments are enforcing regulations to ensure it happens. Modular and wall panel factories that fail to innovate risk being left behind.
Integrating ThermalStuds into your product line not only helps meet these demands but also positions your factory as a forward-thinking leader in the market. Here’s how:
Stay Ahead of Regulations: Energy codes are only going to get tougher. ThermalStuds provide a long-term solution that keeps your factory ahead of the curve.
Enhance Marketability: Builders and developers are actively seeking products that simplify energy compliance. By offering panels and modules with integrated ThermalStuds, your factory becomes their go-to supplier.
Reduce Callbacks: Energy code failures can lead to expensive callbacks and retrofits. ThermalStuds ensure your products meet standards right the first time.
Gain a Competitive Edge: Factories that adopt cutting-edge materials like ThermalStuds signal to clients that they are committed to quality, efficiency, and innovation.
Real-World Applications and Success Stories
Factories that have incorporated ThermalStuds are already reaping the benefits. For instance, a modular home factory in the Midwest recently revamped its product line to include ThermalStuds in all exterior walls. The result? A 30% reduction in insulation costs, faster approval on energy code compliance, and an uptick in orders from energy-conscious developers.
Similarly, a wall panel manufacturer in the Pacific Northwest used ThermalStuds to create a new line of high-performance panels. Their streamlined design enabled builders to meet Passive House standards without adding costly exterior insulation, resulting in increased demand from green-building contractors.
These case studies underscore the versatility and effectiveness of ThermalStuds in real-world scenarios.
Overcoming Barriers to Adoption
Like any innovation, adopting ThermalStuds may come with initial hesitations. Concerns about cost, compatibility, or production changes are valid but manageable. In reality, the investment in ThermalStuds pays off quickly through savings in material costs, reduced labor, and increased market share.
Manufacturers like Brian Iverson, the innovator behind ThermalStuds, have gone to great lengths to ensure their product is factory-friendly. Training, support, and compatibility testing are readily available to help your factory make a smooth transition.
The Bottom Line: Build Smarter with ThermalStuds
The modular and wall panel industry is at a crossroads. To thrive in today’s energy-conscious market, factories must adopt materials and processes that not only comply with regulations but also streamline production and reduce costs. ThermalStuds check all these boxes.
By investing in ThermalStuds, your factory can transform challenges into opportunities. You’ll not only meet energy codes with ease but also deliver superior products that builders and developers can trust.
So, what are you waiting for? The future of construction is here—and it’s framed with ThermalStuds.
Reader interactions
3 Replies to “Building the Future: Why Modular and Wall Panel Factories Need ThermalStuds to Meet Energy Codes with Ease”
I applaud the concept, but I would recommend modular manufacturers look at the naked thermal studs (uninsulated cavity). Space them 24″ OC and install closed cell spray foam in the cavity and “through” the thermal stud on your production line(s). Improved racking strength benefits, R-30 2X4 walls, no thermal bridging and no transportation damage. Lighter weight due to reduced lumber and every faming member is now thermally broken including walls, floors and roof assemblies. If manufacturers want a spray foam integrator – give me a call (it’s what I do). http://www.letstalkpur.com, [email protected]
I plan on using thermal studs in building 2 homes in Abaco Island, Bahamas. Where do I get them? Is there a price difference between foam between the 2×2 sides, or in the thermal stud with the dowels.
Looking for building by mid-summer.
s
Hi Gordon, feel free to reach out to me in regards to your question. [email protected] is the best email for me. I can help you get in touch with TStud manufacturers.