In an industry facing mounting pressure to balance energy efficiency, structural integrity, and affordability, innovation becomes the key to change. Brian Iverson, the visionary behind Thermal Studs, has taken up this challenge by addressing long-standing inefficiencies and sustainability issues in traditional building materials. The Thermal Studs system emerged as a solution rooted in practicality and inspired by a moment of personal necessity—a broken furnace during the COVID-19 pandemic. Iverson’s vision extends beyond temporary fixes, offering builders a streamlined approach to reduce energy consumption by up to 50% and increase overall building performance.
Brian Iverson, Chief Innovator at Thermal Studs (that’s not a Thermal Stud he’s holding)
At the core of the Thermal Studs initiative lies a simple yet powerful idea: eliminate thermal bridges, enhance structural resilience, and ensure ease of manufacturing for anyone, even from a modestly equipped space like an oversized garage. Through the Thermal Studs Ultimate Panel System (TSUPS), builders and developers gain a robust tool to revolutionize construction processes and energy use. Iverson’s approach combines built-in insulation with structural efficiency to create a sustainable path forward in the building industry—one that is scalable, innovative, and ready to meet the demands of the future.
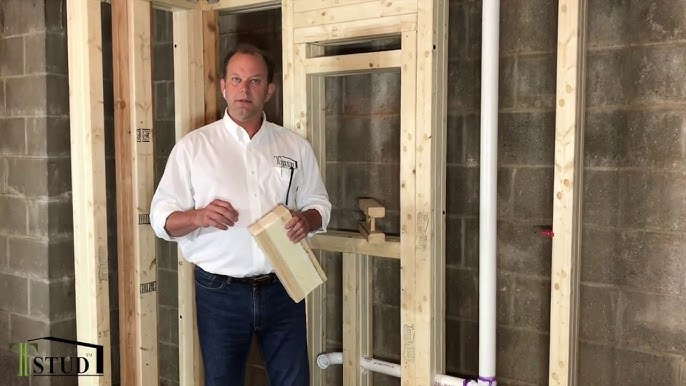
Brian Iverson holding the R19 Tstud
I recently had the opportunity to talk with Brian about his latest innovation:
Gary Fleisher: What specific problem in the building industry inspired you to develop Thermal Studs, and how does your solution address it in ways that current options cannot?
Brian Iverson: The building industry faces a clear challenge: the need for energy-efficient solutions that reduce heating and cooling costs, improve structural integrity, and promote sustainability—all while remaining affordable. Traditional framing materials often fail in these areas, leading to higher energy costs, moisture problems, and compromised comfort.
I developed the Thermal Studs product line to tackle these issues head-on. It started with a simple realization: during the COVID-19 pandemic, I experienced a furnace malfunction and couldn’t find the replacement part. It’s called a “critical supply chain” challenge. That was when I decided to create a better, more cost-effective solution. The result? Thermal Studs, a system that combines built-in insulation and structural strength, reducing energy consumption by up to 50%. The beauty of the Thermal Studs Ultimate Panel System (TSUPS) is its simplicity—anyone with a spray foam rig and carpentry tools can build the Thermal Stud products, even in an oversized garage.
With Thermal Studs, we know how to eliminate thermal bridges and inefficiencies found in conventional framing methodologies, providing a high-performance, sustainable building system that can be replicated without reliance on complex supply chains. This is a game-changing licensing opportunity for builders, lumberyards, etc., to take control of their construction process and solve for energy efficiency while reducing the lifetime utility bills for their customers. Now that was a mouthful.
Gary: Could you walk us through the core technology or materials behind your inventions?
Brian: The core technology behind Thermal Studs is the integration of closed-cell foam insulation with innovative structural configurations that enhance both thermal efficiency and structural strength. Our products, such as the WarmStud™, RhinoStud™, and Tstud™, utilize non-commodity materials to optimize performance, providing solutions that go beyond traditional building materials. And for those who do not want the foam component, we have the Un-Insulated Tstud™ as well.
For example, the metal RhinoStud™ incorporates a serpentine design combined with a built-in Z Girt system, which together create an effective thermal buffer that slows down heat transfer. While not a true thermal break, the foam layers surrounding the metal stud significantly reduce thermal bridging, offering superior thermal efficiency. This unique system also provides enhanced load resistance, allowing the RhinoStud™ to support up to 100% more axial compression weight of a typical metal C Shaped stud. Additionally, it offers excellent sound control and meets rigorous seismic and hurricane compliance standards.
The WarmStud™ delivers an affordable solution for achieving 100% continuous insulation, making it the most cost-effective choice for energy-efficient building. The Tstud™ outperforms LVL studs in terms of strength and resilience, offering enhanced performance for structures that need to withstand extreme conditions.
These innovations are designed to exceed energy codes across North America, ensuring that homes and buildings are both energy-efficient and structurally sound. The result is a sustainable building system that empowers today’s builders to create high-performance structures without sacrificing affordability.
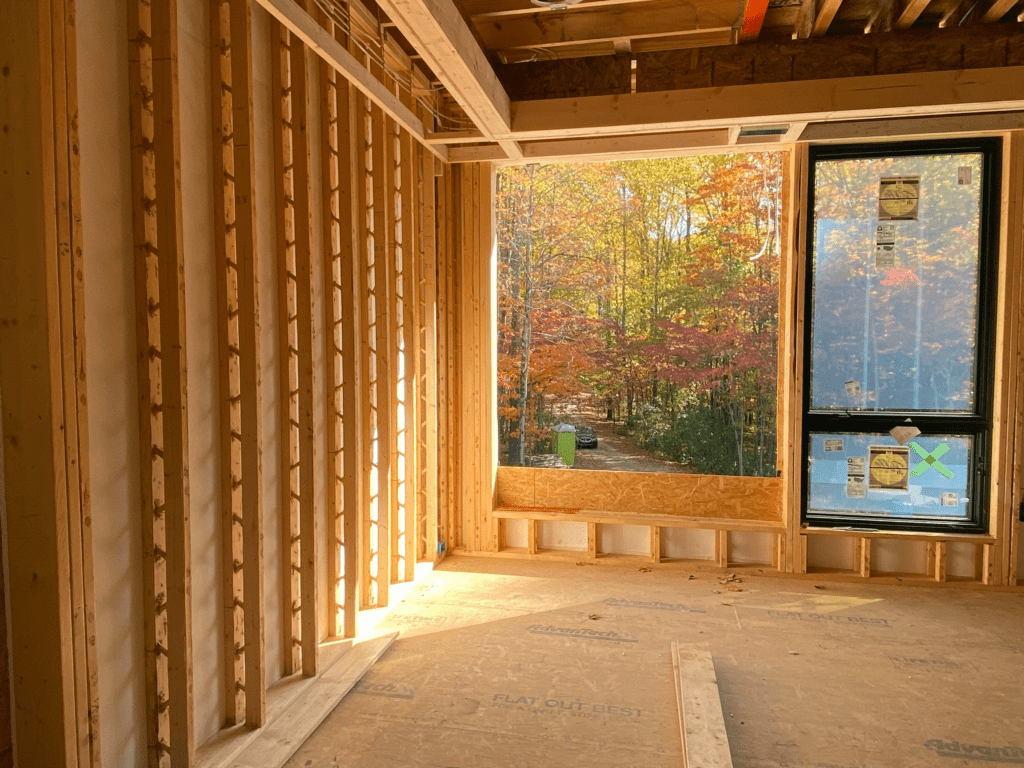
Gary: What makes them unique, or groundbreaking compared to traditional building materials or methods?
Brian: To reduce heating and cooling loads by ~50% or more, a fully integrated solution is necessary—one that combines insulation, structural strength, and sustainability. The Thermal Studs individual products and now the newly invented Thermal Studs Ultimate Panel System (TSUPS) is just that. It integrates all three in a way that traditional available materials can’t match.
Unlike conventional materials that require multiple components from various suppliers, Thermal Studs components can be sourced from anyone—foam, studs, nails, and screws from any supplier—and still deliver an industry-leading solution. You can even build walls up to 20 feet tall using our system. Moreover, the Tstud™ products feature a double thermal break when incorporated into the TSUPS, providing enhanced protection against extreme weather and drastically reducing energy loss.
The Thermal Studs Ultimate Panel System not only addresses thermal inefficiencies but also ensures long-term durability, creating a more resilient and eco-friendly building solution.
Gary: Building materials must meet strict regulatory standards. What challenges did you face in bringing your products to market?
Brian: Creating building materials that meet stringent regulatory standards was one of our biggest challenges. My goal was to design products strong enough to withstand the toughest conditions, whether hurricane-level winds or seismic activity, all the while avoiding the complexity of dozens of SKUs for different regions.
The real challenge was the production side. I’m not a manufacturing expert, which is why we rely on licensing for others to produce the products. It wasn’t just about developing the right solution; it was about figuring out how to get it to market and make it a business. Supply chain disruptions and delays in production equipment only added to the complexity. But through it all, we stayed focused on creating an easy-to-use, compliant, and affordable solution that could stand up to any regulatory standard.
Any Parting thoughts, Brian?
As the “old fart” who’s invented all of this, I’m too old to manufacture and I couldn’t get 20 people to sing kumbaya anyway. So, we’re licensing these game-changing solutions to anyone ready to take them to the next level. You get proven, high-performance products, and we get to support your successes. The opportunity is clear: manufacture Thermal Studs products with minimal upfront investment. With our TSUPS (Thermal Studs Ultimate Panel System), anyone with an existing facility can build these solutions. It’s an easy entry into the market, and we’re offering licenses for both the products individually or TSUPS wall, roof, and floor panel manufacturing, giving entrepreneurs a low-cost, high-reward chance to get started fast. If you’re ready to join us and make the future of construction as strong as the Thermal Studs we’ve created, let’s make it happen!
Look for Part Two of our conversation coming soon