How “Modern Methods of Construction” Became an Innovative Catch-All Buzzword—and Why That’s a Problem
Few acronyms are thrown around the offsite construction industry with more frequency—and less clarity—than MMC. Short for Modern Methods of Construction, MMC is used in government reports, developer brochures, LinkedIn posts, and startup pitch decks. It’s the industry’s go-to phrase for signaling innovation, speed, and disruption. But beneath the glossy surface lies a surprising truth: nobody seems to agree on what MMC actually means.
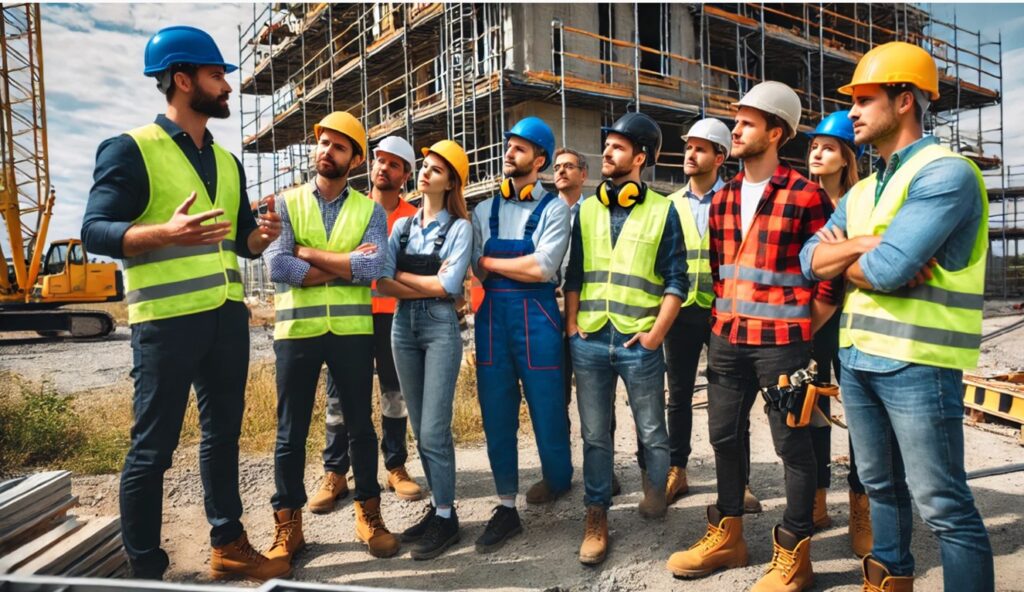
“We’re going to use MMC on this project. Who knows what that means?”
In fact, the term has become so broad and diluted, it risks doing more harm than good—confusing investors, misleading developers, and overselling innovation.
So where did MMC come from? Why did it catch on? And how can the offsite construction industry reclaim its meaning?
Origins: From War Recovery to Policy Buzzword
The idea behind MMC isn’t new. In the aftermath of World War II, countries like the UK faced a desperate housing shortage. To accelerate rebuilding, they experimented with non-traditional building systems: prefabricated homes, concrete panels, and mass housing estates built in record time.
But the modern use of the term MMC emerged in the early 2000s, particularly in the UK, when policymakers began to focus on accelerating housing delivery using new technologies. Rather than promote one method over another, they coined “Modern Methods of Construction” as an umbrella term for any technique that significantly improved upon traditional on-site, brick-and-mortar building methods.
It was never meant to be a single method. Instead, MMC was a category of promise—innovation, efficiency, and sustainability wrapped into one tidy phrase.
The Flexibility That Became Its Flaw
In theory, MMC’s broadness was a strength. It could include:
- Volumetric modular construction
- Panelized systems
- Precast concrete elements
- Structural Insulated Panels (SIPs)
- Bathroom and kitchen pods
- Robotic bricklayers
- 3D-printed components
- Even digital tools like BIM or automated manufacturing
But in practice, that flexibility became confusion. Over time, MMC began to mean everything and nothing.
One builder uses it to describe a highly engineered modular system with robotic automation. Another uses it to describe traditional wood framing done slightly faster in a warehouse. A third says they’re using MMC because they’ve adopted QR codes for inventory tracking.
Where’s the line between “modern” and “just marginally better”? There isn’t one—because no one ever defined it.
The UK Tried to Fix It—Sort Of
In response to this ambiguity, the UK government introduced a seven-category MMC framework to provide clarity. The categories range from Category 1 (volumetric modular systems) to Category 7 (site process improvements).
This attempt to structure the MMC conversation was a step in the right direction. But it also revealed the challenge: the term covers such a wide spectrum that it becomes difficult to measure impact or compare methods.
Is a site-built home using offsite-manufactured roof trusses really practicing MMC? According to some categories, yes.
That kind of grey area frustrates developers, complicates compliance, and often dilutes the innovation message.
In the U.S. It’s Even More Vague
In the United States, MMC is used far less formally. There’s no standardized framework. Most U.S. builders and developers use “modular,” “offsite,” “prefab,” or “industrialized construction” to describe what they do—and MMC gets tossed in as a catchphrase to sound cutting-edge.
Startups love it. Investors love it. But few stop to ask: What exactly makes this method “modern”? Compared to what?
Without standards, “MMC” becomes a label of convenience, slapped onto any process that wants a bit of futuristic flair.
Why It Matters
So what’s the harm?
When a term like MMC becomes overused and underdefined, several problems arise:
- Investors get confused. They back companies that say they’re using MMC but don’t understand the difference between a volumetric startup and a panelized one with high overhead and long lead times.
- Developers make false assumptions. They think MMC always means faster, cheaper, and easier. When delays or on-site rework occur, faith in the method erodes.
- Governments misallocate incentives. Without clear definitions, funding programs or tax credits aimed at supporting innovation may end up supporting outdated systems.
- Builders lose trust. The entire category takes a reputational hit when one “MMC” project fails, regardless of the underlying method.
What MMC Should Mean
If MMC is to remain useful, it needs to be anchored to outcomes. It should represent a demonstrable improvement over traditional construction in one or more of the following areas:
- Speed: Measurable reduction in build times
- Efficiency: Less material waste, fewer labor hours
- Safety: Reduced on-site risk and exposure
- Sustainability: Lower carbon footprint and energy use
- Quality: Factory-controlled precision with higher standards
- Cost predictability: Less pricing volatility and fewer change orders
And those benefits should be quantifiable, not just claimed.
The Industry’s Path Forward
So what can we do to ensure MMC becomes meaningful again?
- Use more specific language. Say “volumetric modular” or “closed panel timber frame” instead of just MMC.
- Demand evidence. Ask vendors and builders to show measurable performance improvements, not just buzzwords.
- Educate stakeholders. From investors to city inspectors, help others understand what MMC really entails.
- Adopt shared frameworks. Whether it’s the UK’s MMC categories or a U.S.-specific version, the industry needs shared definitions to compare apples to apples.
- Call out misuses. When a traditional method is dressed up as “modern” without meaningful change, we should say so.
Your Thoughts: Define or Ditch
MMC was born out of necessity—a way to group construction innovation into a digestible concept. But now it’s drifting toward meaningless marketing jargon.
We have two choices: define it properly or stop using it altogether. Because without precision, MMC doesn’t help us move forward. It just muddies the waters.
If you’re truly building better, faster, and smarter, say so. But say how. Because “modern” isn’t a magic word—it’s a measurable outcome.
.
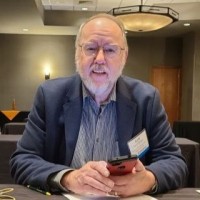
Gary Fleisher
Gary Fleisher is the Leading Observer of the Offsite Housing Construction Industries. He has been actively involved in researching and writing about the latest trends and developments in the industry for over a decade now.
With his extensive knowledge and experience, Gary has emerged as a go-to expert for businesses looking to stay ahead of the curve in the modular construction industry. In addition to his work as an editor, he is also a sought-after speaker and consultant who has helped numerous companies achieve strategic and operational success.