FRAMECAD is one of the worlds leading innovators in automating cold formed steel framing construction. Their claim of being “relentless innovators” caught my eye so I contacted Curtis Edgecombe, who is the Senior Vice President of FRAMECAD Americas. Is it a viable alternative to wood frame offsite construction? Read below, it just may get the proverbial wheels turning.
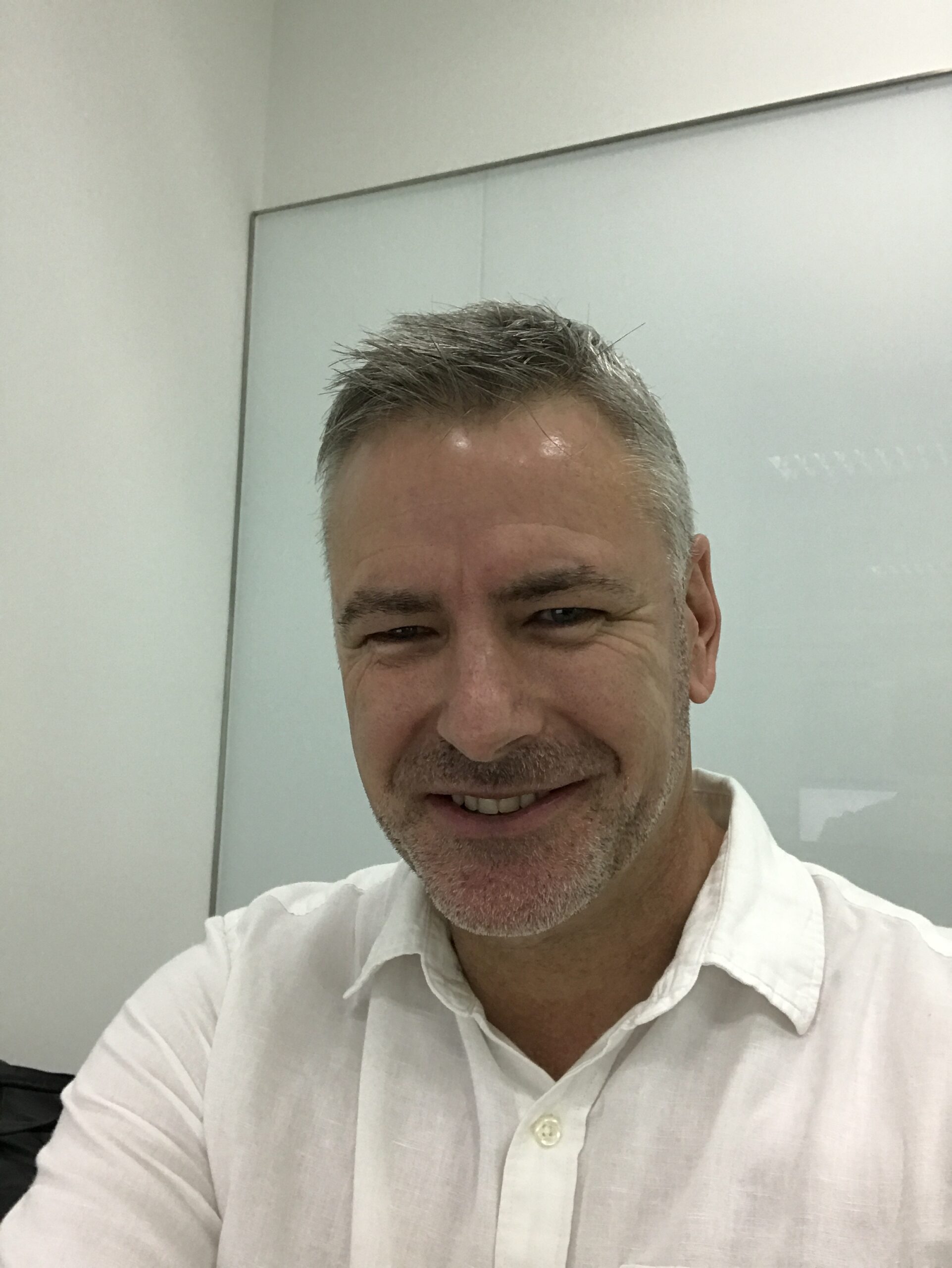
Curtis Edgecombe, Executive VP, FrameCad
Bill Murray, Offsite Innovators: Can you give us a brief overview of what FRAMECAD does and the role it plays in the offsite construction industry?
Curtis Edgecombe Framecad: For more than 35 years, FRAMECAD has been a leader in steel frame building innovation. We provide end-to-end steel framing systems and the framework to simplify and automate cold-formed steel (CFS) framing construction, from design and engineering to manufacture, build and delivery to the job site. FRAMECAD’s ecosystem of manufacturing equipment and solutions delivers CFS framing faster and more sustainably, with a lower total cost of ownership and the resilience to withstand the test of time.
We see a tremendous opportunity for CFS to impact the future of construction and play a significant role in addressing the need for more sustainable, resilient and affordable structures. As developers, owners and AEC professionals seek ways to overcome market challenges and build faster, affordably and sustainably, FRAMECAD offers a proven path to structures that not only meet the demands of today but are built to last for the next hundred-plus years.
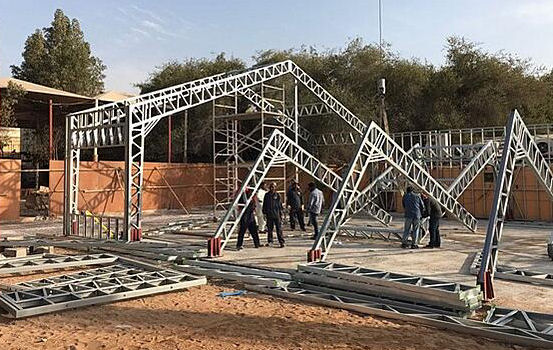
Bill : FRAMECAD is headquartered in Auckland, New Zealand. What are your major markets currently and how do you serve these markets?
Curtis: FRAMECAD was founded in 1987 with a mission to put a roof over peoples’ heads. From humble beginnings selling roofing products in New Zealand, the company has grown and evolved to offer a full end-to-end solution for residential and commercial construction projects worldwide in over 120 countries and over 1000 FRAMECAD systems. We have a global network of local experts to support our customers. We recently opened a Customer Success Center in Las Vegas, Nevada, to provide live demonstrations and education to customers in the US.
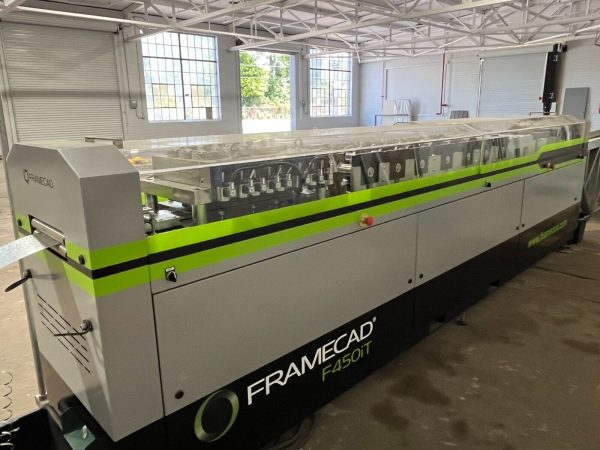
.
Bill: At the heart of the matter is the cost effectiveness of CFS compared to wood frame construction. Can you speak to the cost effectiveness of CFS, both upfront and over the total cost of a project?
Curtis: The design-led process and precision manufacturing of CFS framing components minimize waste and allow for a more sustainable construction process with lower material costs. Because they are manufactured with precision, CFS panels and components are easy to assemble and come together seamlessly with less labor required on site.
CFS’ durability, strength and ability to withstand extreme climate events reduce risk for contractors. The non-combustible nature of steel significantly lowers the risk of fire-related incidents, a primary concern for insurance providers. By opting for steel framing, developers and builders can benefit from substantially lower builder’s risk insurance premiums. These savings can be considerable, particularly for large-scale projects where insurance costs constitute a significant portion of the budget. The use of steel-framed products can reduce premiums by 25 to 75 percent.
Unlike wood, which can be subject to variations in standards due to factors such as knots and grain patterns, the strength and durability of CFS are consistent—the reliability and predictability of CFS results in projects with less rework and costly construction delays.
The durability of CFS framing reduces the need for maintenance for a lower total cost of ownership. It leads to fewer claims related to damage from pests, rot and structural failures, which lowers insurance costs. Over time, the cumulative savings from reduced insurance premiums and maintenance costs can substantially affect a building’s overall cost.
The fast, accurate production and assembly of steel framing and the ability to build multiple components simultaneously also result in significant savings. Craning the components into place saves on safety precautions, scaffolding and insurance costs. This accelerated construction cycle reduces the total project cost and allows owners to occupancy buildings more quickly.
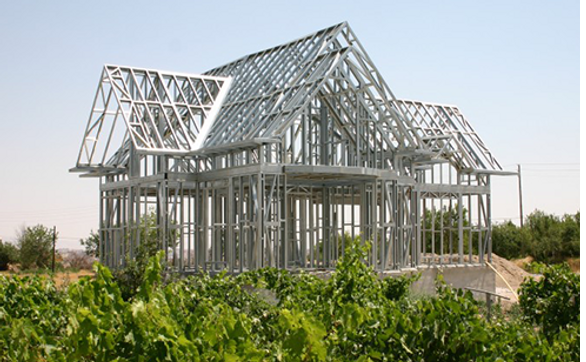
.
Bill: CFS is often perceived as less sustainable or environmentally friendly than wood. How does FRAMECAD approach sustainability in its processes and materials?
Curtis: While CFS framing is sometimes seen as less sustainable than wood, FRAMECAD integrates sustainability into every aspect of its construction process. Our precision-driven, offsite manufacturing minimizes waste, and our advanced design software ensures optimal material use.
CFS structures are also highly energy-efficient, reducing environmental impact over their lifespan. Its durability ensures long-term sustainability, as they are adaptable to climate extremes, requiring fewer repairs or replacements. This resilience reduces resource consumption and helps buildings maintain their performance for decades.
Additionally, steel is 100% recyclable. At the end of a building’s life, the material can be recycled and repurposed to create new structures, contributing to a circular economy and reducing the need for virgin raw materials.
At FRAMECAD, sustainability is embedded into our entire process—from design to manufacturing—helping our clients build faster, smarter, and more environmentally responsible structures.
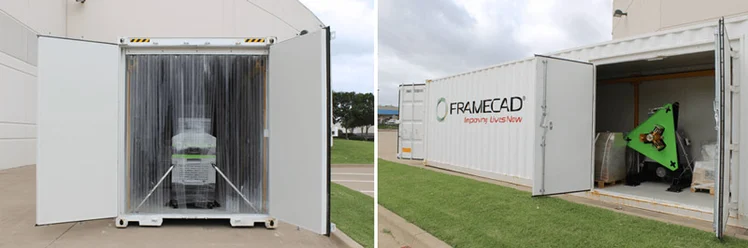
Mobile Factory revolutionises remote and disaster relief construction
Bill: With the rise of modular and prefabricated/offsite construction methods, how does FRAMECAD’s technology enhance efficiency and flexibility in design and construction?
Curtis: FRAMECAD’s end-to-end solution covers the entire CFS process, from design and manufacturing to assembly. Our roll-forming equipment, design and engineering software and production management solution are integrated and open, giving every stakeholder an entry point to take advantage of the benefits of CFS whether they use FRAMECAD’s design software or other design software from providers such as Autodesk, Structsoft, Tekla Structures or Vertex.
Our goal is to make it easy for owners, developers and manufacturers to take advantage of CFS steel framing, so we offer files from any design software to feed production-ready data into the FRAMECAD ecosystem.

Our latest innovation, Nexa, is the first end-to-end production management platform designed specifically for cold-formed steel framing. With Nexa, cold-formed steel manufacturers have complete visibility into operations and real-time project data for complete control from the factory to the job site. With a single platform for project management, factory operations and jobsite efficiency, manufacturers can deliver projects faster, with less waste and more predictability. Nexa gives manufacturers the visibility they need for seamless communication and collaboration with contractors and owners, building trust from start to finish.
Bill: What are the major hurdles to overcome in growing the CFS offsite industry?
Curtis: Despite the proven benefits of offsite manufacturing, which include repeatability, less reliance on skilled labor and schedule efficiencies, less than 4 percent of current U.S. housing stock is built using modular techniques. Change is difficult, and for many in the construction industry, doing things as they’ve always been is perceived as easier.
And yet, construction projects are most often over budget and behind schedule. A shortage of skilled labor, the pressure of climate events calling for more resilient structures, tremendous waste in construction processes and practices, and the responsibility for a more sustainable future beg for a solution. We’ve reached a tipping point, and it’s time for a better way to build.
The combination of offsite construction and cold-formed steel offers a solution to owners and developers frustrated by wasteful, delayed and over-budget projects.
The biggest barrier is visibility among developers and owners, as well as educating architects and engineers to consider steel framing as a design alternative.
Bill: What are some notable projects or partnerships that highlight the strengths of FRAMECAD’s systems?
Curtis: Industrialized Construction Solutions (ICS) engineers, designs, and manufactures prefabricated buildings across the US.
When the company opened its doors 17 years ago, it primarily focused on prefabricated panelized penalized wood buildings. In search of a solution for a shrinking labor force and complicated supply chains, ICS started exploring the applicability of CFS to its design, engineering and delivery and discovered FRAMECAD.
ICS adopted CFS for its stability and resilience benefits over wood. Today, ICS partners with manufacturers who use FRAMECAD equipment to produce CFS designed for seamless manufacturing, assembly and installation in the field. The speed, efficiency, and precision lead to a higher quality product than what general contractors traditionally see arriving at the site.
The FRAMECAD network is critical to the success of ICS. The company works with multiple manufacturers nationwide that use FRAMECAD, allowing it to deliver a standard product with constant quality through multiple vendors.
Bill: Thanks to Curtis for an introduction to an innovative world leader in CFS offsite construction. The FRAMECAD website is extremely informative and I encourage our readers to visit the site—it just may present a highly sustainable alternative to the way we’ve been building for the last 100+ years!