AI-Controlled Image Processing: A Innovative New Investment for Modular Home and Component Factories
The modular construction industry stands at the threshold of a technological revolution. While automation has streamlined many aspects of factory production, a critical area still ripe for innovation is real-time quality control and process optimization. One of the most promising advancements is AI-controlled image processing, also known as machine vision, which uses artificial intelligence and advanced imaging to enhance efficiency, reduce waste, and improve overall product quality.

.
As modular home and component factories evolve, integrating AI-powered industrial image processing can fundamentally change how production lines operate. From ensuring precise cuts in panelized walls to detecting micro-defects in cross-laminated timber (CLT) or structural insulated panels (SIPs), machine vision is poised to bring a new level of intelligence and automation to offsite manufacturing.
What is AI-Controlled Image Processing?
At its core, AI-controlled image processing involves capturing and analyzing 2D or 3D images of components in real-time to extract valuable information and make instant decisions based on detected anomalies, measurements, or quality deviations. This is accomplished using high-resolution cameras, infrared sensors, LiDAR, and AI-driven algorithms that analyze images faster and more accurately than human inspectors ever could.
Framebotix, with its advanced AI-driven software solutions for robotic automation in construction, is uniquely positioned to enhance AI-controlled image processing in modular and component factories. By integrating its real-time computer vision and adaptive learning algorithms, Framebotix can enable precise defect detection, automated measurement validation, and seamless robotic guidance on the production line. Its software can analyze high-resolution images and 3D scans to detect material inconsistencies, ensure accurate fastener placements, and optimize cutting patterns—all in real time. By bridging AI-powered quality control with robotic automation, Framebotix helps modular factories increase efficiency, reduce waste, and maintain consistently high product standards.
This technology is already transforming automotive and electronics manufacturing, and now, it is ready to redefine modular home and component factories by offering a smart, self-correcting production process.

.
Applications in Modular Construction and Component Factories
1. Real-Time Quality Control on the Production Line
One of the biggest challenges modular factories face is ensuring that every component meets precise specifications. Traditional quality control relies on manual inspection, which is time-consuming, prone to human error, and often reactive rather than proactive.
With AI-powered machine vision, every panel, module, or component can be inspected in real time. Cameras and sensors placed at strategic points along the production line can:
- Identify dimensional inaccuracies in prefabricated walls, floors, or roof panels before they proceed to the next stage.
- Detect cracks, warping, or knots in engineered wood and CLT panels before assembly.
- Verify structural connections in steel or timber frames using 3D scanning technology.
By catching errors at the source, factories can significantly reduce rework, minimize waste, and improve product consistency.
2. Automated Precision Measurement for Modular Components
Each modular unit or panelized wall must be cut, drilled, and assembled with extreme precision to ensure seamless integration on-site. Even a 2mm deviation can cause major alignment issues when stacking multiple modules or fitting doors and windows.
Machine vision systems with sub-millimeter accuracy can:
- Measure cut-outs for MEP (mechanical, electrical, plumbing) openings to ensure perfect alignment before installation.
- Verify that insulation is evenly placed in SIPs or CLT wall panels.
- Ensure screw and fastener positioning is consistent across all units.
This level of real-time measurement and correction is critical in high-speed, high-volume modular factories, where precision directly impacts final assembly.
3. AI-Powered Defect Detection in Materials
Many modular builders use engineered wood, SIPs, CLT, and advanced composite materials. Detecting hidden defects in these materials—such as internal cracks, moisture pockets, or adhesion failures—is difficult with the naked eye but easy with AI-driven imaging.
- Infrared and ultrasonic imaging can detect invisible defects in timber or SIP adhesives.
- AI algorithms can assess grain orientation and fiber quality to predict weaknesses before components go into production.
- Thermal imaging can identify heat leaks in insulation panels, preventing costly rework down the line.
The ability to detect material failures before they compromise structural integrity ensures higher-quality modules and reduces warranty claims.
4. Streamlining Assembly and Robotic Integration
AI-controlled image processing doesn’t just spot errors—it actively optimizes workflows by guiding automated machinery and robotic systems.
- Automated robotic arms can be trained to follow AI-generated visual markers, ensuring precise material placement and fastening.
- Vision-guided robotic welding can improve structural connections in steel modular frames, ensuring long-term durability.
- Augmented reality (AR) overlays on factory floors can assist human workers in following exact assembly steps, reducing training time and errors.
The result? Faster production cycles, fewer human errors, and an overall increase in factory efficiency.
Unlocking the Future: AI-Driven Production Insights
Beyond real-time quality control, AI-driven machine vision can provide deep analytical insights that help factories optimize production over time. By analyzing thousands of images per day, AI can detect patterns of recurring defects, inefficiencies, or potential machine failures.
For example:
- If a certain saw or CNC router starts producing misaligned cuts, AI can predict tool wear before the issue becomes a production bottleneck.
- If thermal imaging repeatedly detects heat leaks in insulated panels, the factory can re-evaluate insulation density or adhesive application.
- If AI identifies common defects among different batches of CLT panels, suppliers can be held accountable for material inconsistencies.
This predictive intelligence allows modular factories to transition from reactive problem-solving to proactive optimization.
Challenges and Considerations
While AI-controlled image processing offers huge advantages, it does require investment and adaptation. Some key challenges include:
- Initial setup costs: Installing high-resolution cameras, LiDAR systems, and AI software requires upfront investment.
- Workforce training: Employees must learn how to interpret AI insights and integrate machine vision into existing workflows.
- Data integration: AI systems need to be linked with factory management software to provide real-time insights and decision-making.
However, as AI-driven manufacturing becomes more standardized and cost-effective, early adopters in the modular construction industry will gain a significant competitive advantage.
Final Thoughts: The Smart Factory of Tomorrow
The modular and offsite construction industry is on the brink of a technological transformation. AI-controlled image processing is not just an improvement—it’s a necessity for factories looking to compete in an increasingly automated world.
By implementing real-time defect detection, automated precision measurement, and AI-driven insights, modular home and component factories can:
- Reduce waste and rework costs
- Increase assembly speed and accuracy
- Enhance product quality and consistency
- Predict and prevent production failures
The future of modular construction belongs to those who embrace AI and automation. The question is no longer if machine vision will be adopted—it’s who will use it best to redefine the industry.
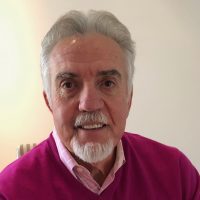
Bill Murray
Bill Murray has over 40 years of operational management experience in the Modular industry. Bill began his Offsite career as a contractor/builder. He then entered the manufacturing side quickly advancing through the sales ranks to become a General Manager/COO of multi plant operations. Bill provides professional advisory service to owners, prospective owners and builder developers considering Offsite construction. He has consulted throughout the U.S., and Mexico, as well as overseas assignments.