The Future of Housing: What the Next Generation Wants vs. What They Will Have to Accept
No matter what we do today, this scenario is becoming their reality
In just two decades, the latest Gen Z and earliest Gen Alpha will enter their 30s, looking for homes, stability, and the fulfillment of the American Dream—or at least, whatever version of it remains. But the housing landscape they will encounter will be vastly different from what previous generations have experienced.

No matter how many policies we enact today, how much innovation we throw at the problem, or how many think tanks try to predict solutions, one reality is emerging: they will want one kind of housing, but they will have to accept another.
The forces shaping this future—economic trends, technology, climate change, and shifting societal values—are already in motion, making many of these outcomes inevitable. This is what we predict they will desire, and the stark compromises they will likely be forced to make.
What They Will Want: A Vision of Smart, Sustainable, and Affordable Homes
If Gen Z and Gen Alpha could design their perfect housing future, it would likely look something like this:
Homes That Are Sustainable and Energy-Independent
By the time they reach their 30s, climate change won’t be a distant threat—it will be a daily reality. Rising sea levels, heatwaves, and frequent disasters will make energy-efficient homes a necessity, not a luxury. The dream home of 2045 will be:
- Carbon-neutral or energy-positive, generating more power than it consumes.
- Built with sustainable materials like cross-laminated timber (CLT), bio-concrete, or 3D-printed recycled composites.
- Designed for climate resilience, with hurricane-proof structures, self-cooling walls, and flood-resistant foundations.
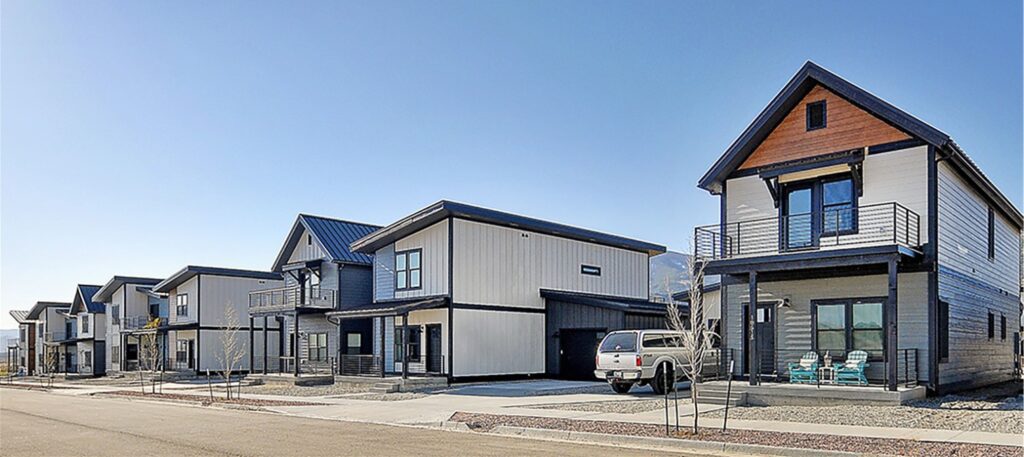
Hyper-Connected Smart Homes
The next generation won’t just want smart homes; they will expect homes that think for them. AI will manage temperature, lighting, security, and even grocery stocking. Workspaces will blend augmented reality (AR) with real-life functionality, and personalized digital assistants will be as crucial as electricity.
Adaptable, Modular, and Flexible Living Spaces
Rigid homeownership models will feel outdated. Future housing will be designed to expand and contract based on life stages, moving away from the static idea of a single home for life. Prefabricated, modular units will allow homes to be reshaped, relocated, or repurposed as jobs and family needs evolve.
Affordable, Shared, and Subscription-Based Housing
For many, the dream will be flexible housing-as-a-service rather than outright ownership. Monthly subscriptions to housing platforms will replace mortgages, offering the ability to move between furnished, networked communities without financial burden. Co-living models will be more accepted as a way to reduce costs and build community.
Urban Convenience Without the Chaos
Gen Alpha will push for 15-minute cities, where everything—jobs, groceries, entertainment, and healthcare—is within walking or biking distance. Public transportation will be dominant, and car ownership will fade, replaced by automated mobility services.
But this is only one side of the coin. Despite these expectations, here’s what they will likely have to accept.
What They Will Have to Accept: A Housing Reality That Won’t Bend to Their Needs
Economic and environmental forces will dictate a much harsher reality despite their preferences.
Homeownership Will Be Out of Reach for Most
By 2045, homeownership will be more unattainable than ever. Rising costs, stagnant wages, and dwindling land availability will push traditional homeownership into the realm of the elite.
- Many will never own property, instead navigating an endless cycle of renting from corporate landlords.
- Real estate monopolization by hedge funds and tech-driven landlords will dominate the market, making affordability even more difficult.
- AI-driven pricing models will make rent unpredictable, fluctuating based on demand and algorithms, much like airline tickets.
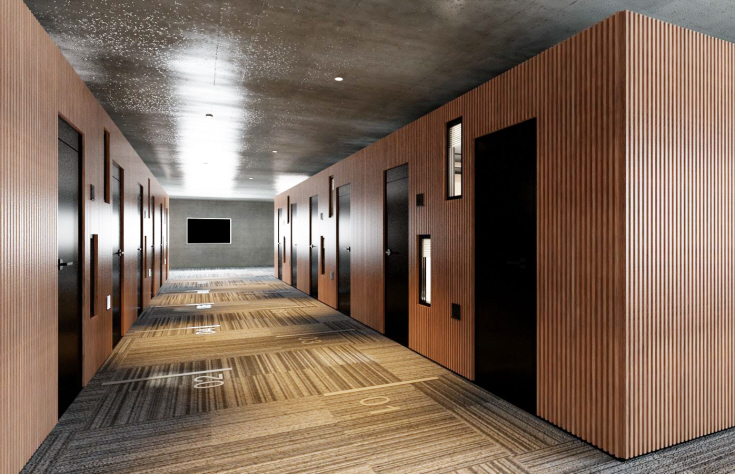
Smaller, Denser Living Spaces
Micro-apartments (under 400 sq ft) will become the norm in high-demand urban areas. Even in suburban developments, space will be minimized as zoning laws and land scarcity make large homes infeasible.
- Multi-generational co-housing may become an economic necessity rather than a choice.
- Tiny homes will not be a fad—they will be a necessity.
- Furniture and walls will need to be collapsible, automated, and multi-use to maximize space efficiency.
Climate-Forced Migration and Resilience Measures
Many of today’s most desirable places to live may not be habitable in 2045. Wildfires, flooding, and extreme weather will force mass migration from coastal cities and heat-stricken regions.
- Floating cities and storm-proof homes will become necessary for some regions.
- Zoning laws will favor vertical living, with high-rise eco-communities replacing sprawling suburban neighborhoods.
- Water rationing, rolling blackouts, and disaster-resistant architecture will become standard in climate-sensitive zones.
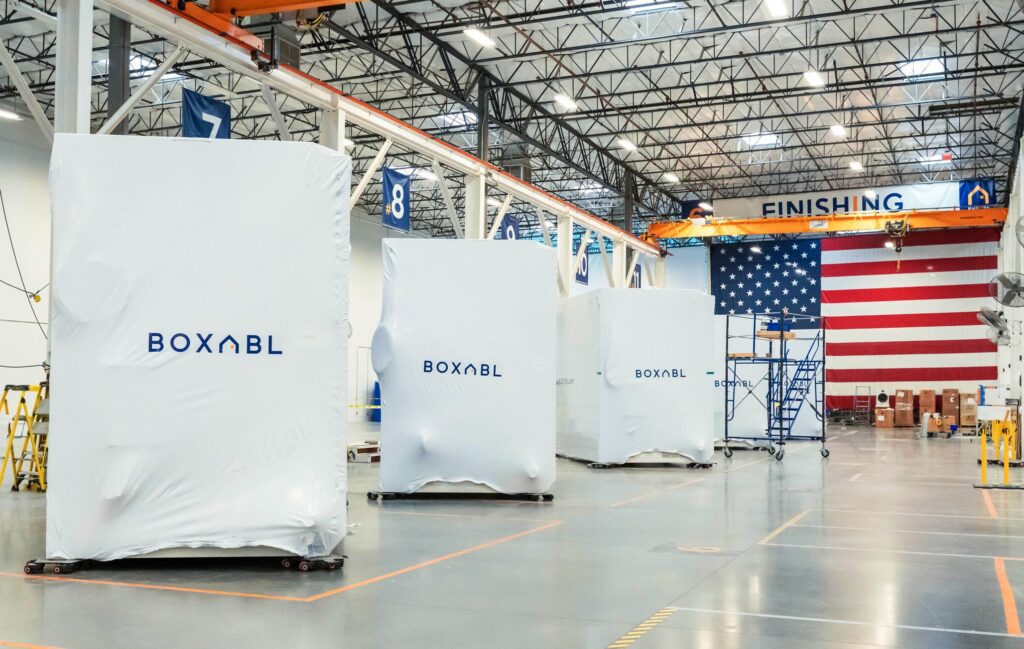
AI-Driven Housing Markets with Less Human Control
The traditional human real estate agent may be extinct by 2045, replaced by AI-managed housing transactions. Everything—from rental applications to pricing and maintenance—will be algorithmically controlled.
- Dynamic pricing for rent will fluctuate based on demand, wealth profiling, and credit scoring.
- Corporate landlords will dominate, reducing the power of individuals to negotiate terms.
- AI-driven mortgage approval systems could either streamline or entirely block access to home loans for many.
Work and Home Will Be Indistinguishable
The future workforce will rely almost entirely on remote and AI-assisted labor, meaning homes must double as full-time workspaces.
- The separation between work and home life will blur even further, increasing stress and burnout.
- Virtual workspaces will be necessary in every home, making dedicated office space a requirement, not a luxury.
- Expect neighborhood co-working hubs instead of large corporate office buildings.
An Unavoidable Reality, Shaped Today
While we can still shape housing policies, land-use regulations, and technological innovation, the fundamental challenges ahead make this reality nearly unavoidable. Economic forces, climate change, and the increasing corporatization of housing are moving faster than most policymakers or urban planners can react.
Gen Z and Gen Alpha will have to redefine success in housing, shifting from ownership-based aspirations to a more flexible, communal, and technology-driven approach. For some, this will mean innovative living solutions and greater adaptability. For others, it will mean forced compromise, less privacy, and fewer personal assets.
This is not speculation. It’s a forecast based on current trajectories—one that policymakers, developers, and industry leaders must confront now if they want to soften the blow.
Because no matter what we do today, this reality is already on its way.
.
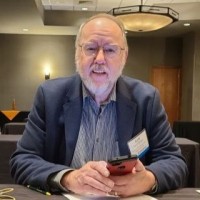
Gary Fleisher
Gary Fleisher is the Leading Observer of the Offsite Housing Construction Industries. He has been actively involved in researching and writing about the latest trends and developments in the industry for over a decade now.
With his extensive knowledge and experience, Gary has emerged as a go-to expert for businesses looking to stay ahead of the curve in the modular construction industry. In addition to his work as an editor, he is also a sought-after speaker and consultant who has helped numerous companies achieve strategic and operational success.