How Reframe Systems Is Disrupting the Construction Status Quo
The construction industry often resists change, but one startup is proving that with vision, engineering, and perseverance, the system can be reimagined—quite literally. San Leandro-based Reframe Systems just won the prestigious 2025 House Building Prize from the Centre for Natural Material Innovation at the University of Cambridge, recognizing their groundbreaking robotic and offsite construction platform. The prize isn’t just a trophy—it’s an acknowledgment that the industry’s old ways are under review, and Reframe’s new approach could be the blueprint for what’s next.
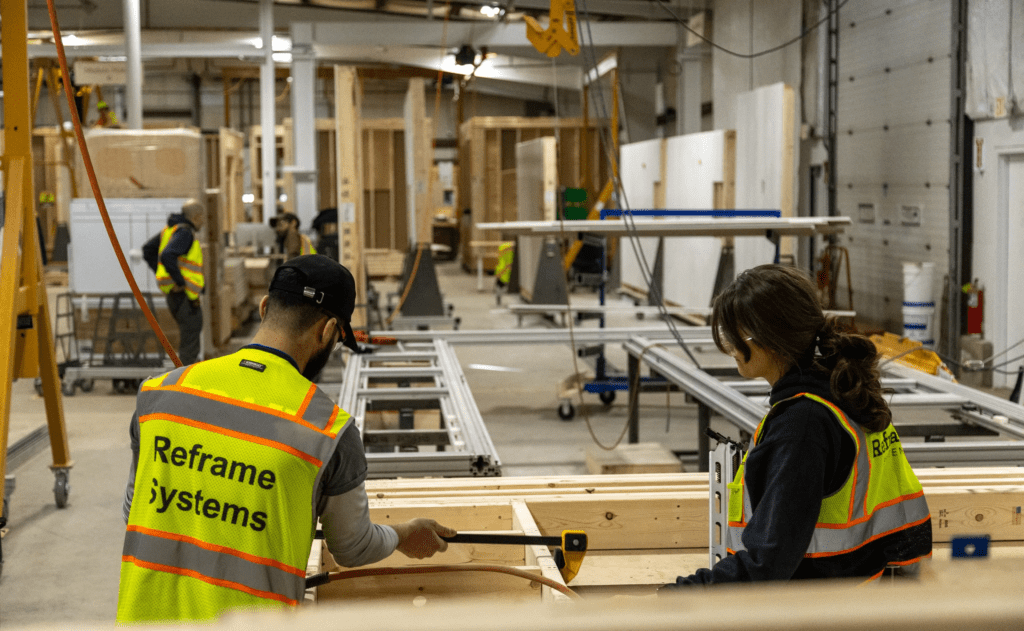
all photos -Reframe Systems
So what makes this company different? The name says it all: Reframe. They’re not tweaking the edges of conventional construction—they’re flipping the entire framing process on its head.
At the Core: A Robotic-First, Offsite-Ready System
Reframe’s approach is built around a modular panelized wall system that’s designed to work seamlessly with both robotic manufacturing and on-site assembly. Unlike traditional prefab systems that rely on lumber-framed panels or heavy volumetric boxes, Reframe’s solution uses robotically produced steel frames that are precise, scalable, and environmentally considerate.
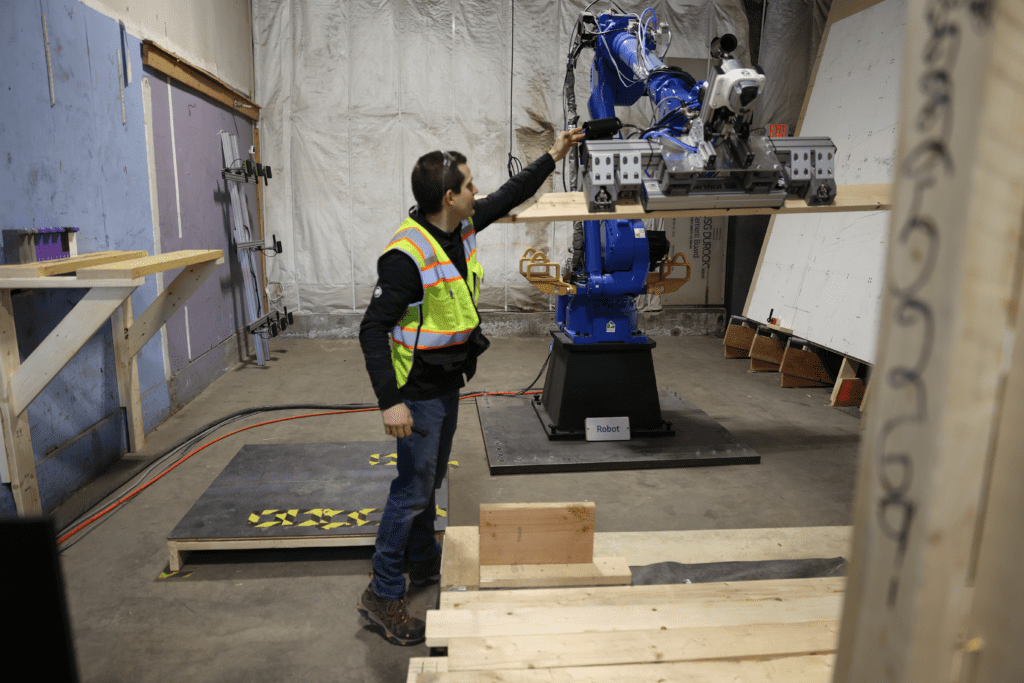
Each panel is a complete building block—pre-fitted with wiring chases, plumbing paths, and insulation compartments. Their innovative connector system makes field installation as easy as snapping components into place. Think IKEA-meets-industrial-engineering—with a focus on high-performance housing.
The result? Buildings that go up faster, with far less labor, tighter tolerances, and improved energy efficiency. And in an industry currently suffering from a global skilled labor shortage, that’s more than innovation—it’s a lifeline.
Designed for Robots, Built for People
Founded in 2022 by a team of software engineers, roboticists, and sustainability advocates, Reframe Systems understood early on that automation had to serve more than just profit margins. Their guiding principle was simple: make housing faster, cheaper, and more sustainable—without sacrificing quality or design.

They began by developing a production system that could combine industrial robotics, AI-driven design software, and advanced materials to streamline every phase of the construction process—from design to delivery. Their factories are essentially smart workshops, where robots build walls that are ready to ship, stack, and install within hours of arriving on-site.
But automation is just the tool. The real value comes from how adaptable the Reframe system is. The panel designs can be configured for multifamily housing, townhomes, ADUs, and even disaster-relief shelters. The platform is scalable, and the technology is open enough to be licensed by other builders—making it possible for developers and general contractors to build more, faster, and with less capital investment than a traditional modular factory.
A Clear Message to the Industry: It’s Time to Catch Up
Winning the House Building Prize from a globally respected institution like the University of Cambridge sends a clear message: Reframe is no longer a “what if”—they’re a “what’s next.”
The Centre for Natural Material Innovation praised Reframe’s “holistic” approach, particularly their use of sustainable materials, efficient structural systems, and their dedication to closing the loop between digital design and physical delivery. The award committee also highlighted the potential impact of the Reframe System on underserved housing markets and its compatibility with low-carbon building goals.
For an industry often mired in regulatory red tape, outdated practices, and fragmented supply chains, Reframe Systems represents a breath of fresh air—and a technological leap forward.
What Comes Next
With their first pilot projects completed and several partnerships in the works, Reframe Systems is scaling up production and actively seeking collaborators. Whether you’re a developer, housing nonprofit, modular factory owner, or investor looking for the next big thing in offsite innovation—this is a company to watch.
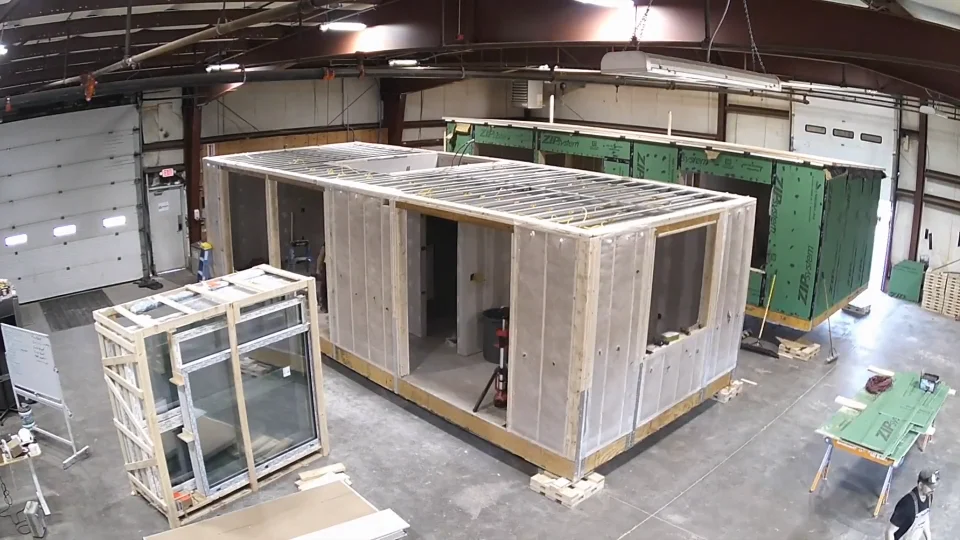
As we continue to explore the innovators shaping tomorrow’s built environment, Reframe Systems reminds us that the future of construction doesn’t need to be built from the ground up—it can be snapped together, robotically manufactured, and radically reimagined.
Learn more at: www.reframe.systems
Offsite Innovators is dedicated to spotlighting the people, products, and platforms redefining how we build. Want your innovation featured? Contact us.