From Trash to Treasure: The New Circular Economy Revolution in Construction
Imagine walking by a demolition site and instead of seeing mountains of concrete rubble and twisted rebar destined for a landfill, you see workers delicately removing windows, carefully unbolting steel beams, and labeling wooden panels for future use. It sounds like a scene from a utopian future, but it’s happening today—and it’s about to change everything we thought we knew about construction.
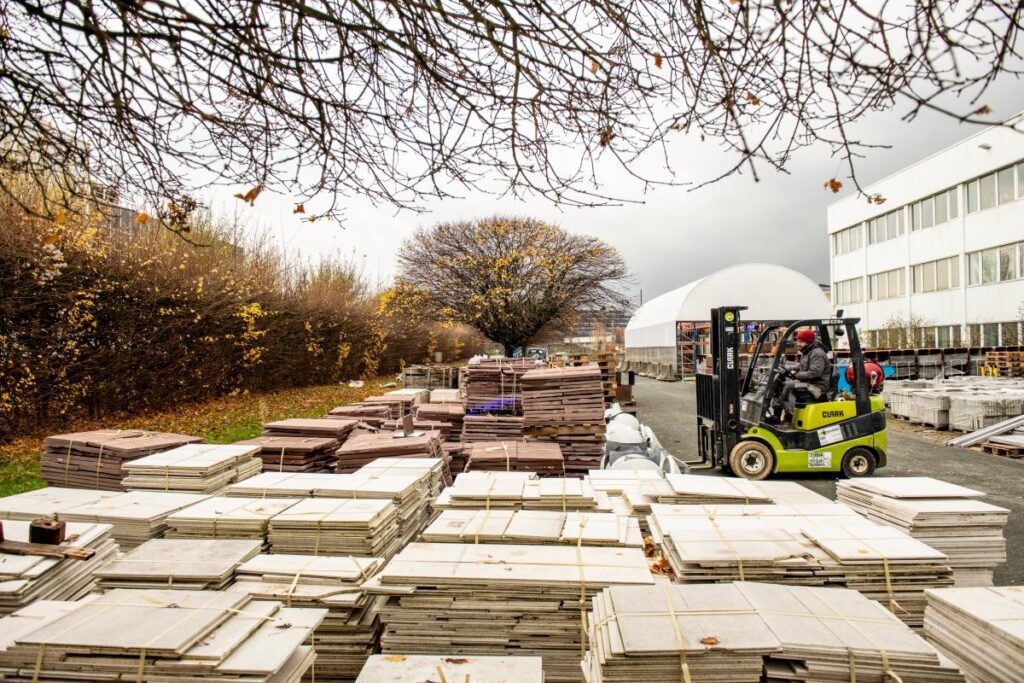
For decades, the construction industry has thrived on a linear model: extract raw materials, build, and demolish when outdated or worn out. This model not only generates about 40% of global waste but also contributes massively to carbon emissions. Yet, a powerful shift is underway—a shift towards the circular economy, where buildings are no longer considered disposable, but rather valuable material banks waiting to be reinvested into future projects.
One company leading this charge is Rotor Deconstruction in Belgium. Instead of wielding wrecking balls, their crews methodically dismantle structures, preserving everything from marble staircases to light fixtures. These salvaged treasures are then sold through their marketplace RotorDC, where architects and builders eager to incorporate sustainable materials can find high-quality, character-rich components. This approach isn’t just green—it’s smart economics. Reclaimed materials often cost less than new, and add unique charm that new products can’t replicate.
Meanwhile, in the United States, Harvest Works partners with contractors to systematically “harvest” reusable components during renovation and teardown projects. Think of it as urban mining—scouring buildings for hidden gems like hardwood floors, steel columns, and vintage doors, then repurposing them instead of burying them under tons of concrete debris.
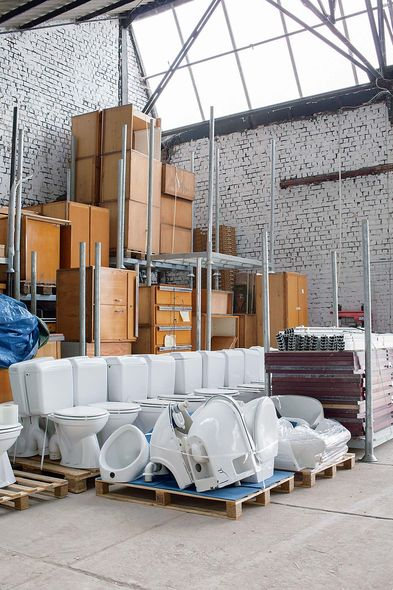
But the circular revolution doesn’t stop at deconstruction. Manufacturers are stepping up too. Global carpet tile giant Interface has pioneered a take-back program where they reclaim used tiles, refurbish them, or recycle them into new products. This kind of closed-loop system doesn’t just reduce landfill waste—it creates a marketing edge and loyal customers who share in the environmental mission.
Knauf Insulation has launched a similar initiative, collecting cut-off scraps and site waste from its mineral wool products to reprocess into new insulation. And over in the Netherlands, Finch Buildings designs modular timber cabins with every panel and component engineered for easy disassembly and reuse. Rather than tearing down entire structures when needs change, these cabins can be relocated, reconfigured, or reimagined.
Beyond corporate programs, online marketplaces like Salvo (UK) and Construction Junction (US) are transforming the way we think about building supplies. These platforms serve as digital bazaars for used and salvaged materials, connecting architects, builders, and DIY enthusiasts eager to blend sustainability with creativity. Imagine designing a sleek modern home using reclaimed oak beams from a 19th-century barn or incorporating vintage tiles from a historic public building—stories and character that new materials just can’t offer.
Driving this momentum is a new generation of architects and developers who see buildings not as static, single-use products but as dynamic repositories of valuable resources. The concept of a material passport, already gaining traction in the Netherlands, catalogs every component in a building, from façade panels to electrical systems, so they can be more easily retrieved and reused at the end of their initial life cycle.
This isn’t just about waste reduction; it’s about rethinking value, creating economic opportunities, and infusing construction projects with new narratives. When we salvage, reuse, and reimagine, we honor the embodied energy and stories of every piece of material, transforming waste into wealth.
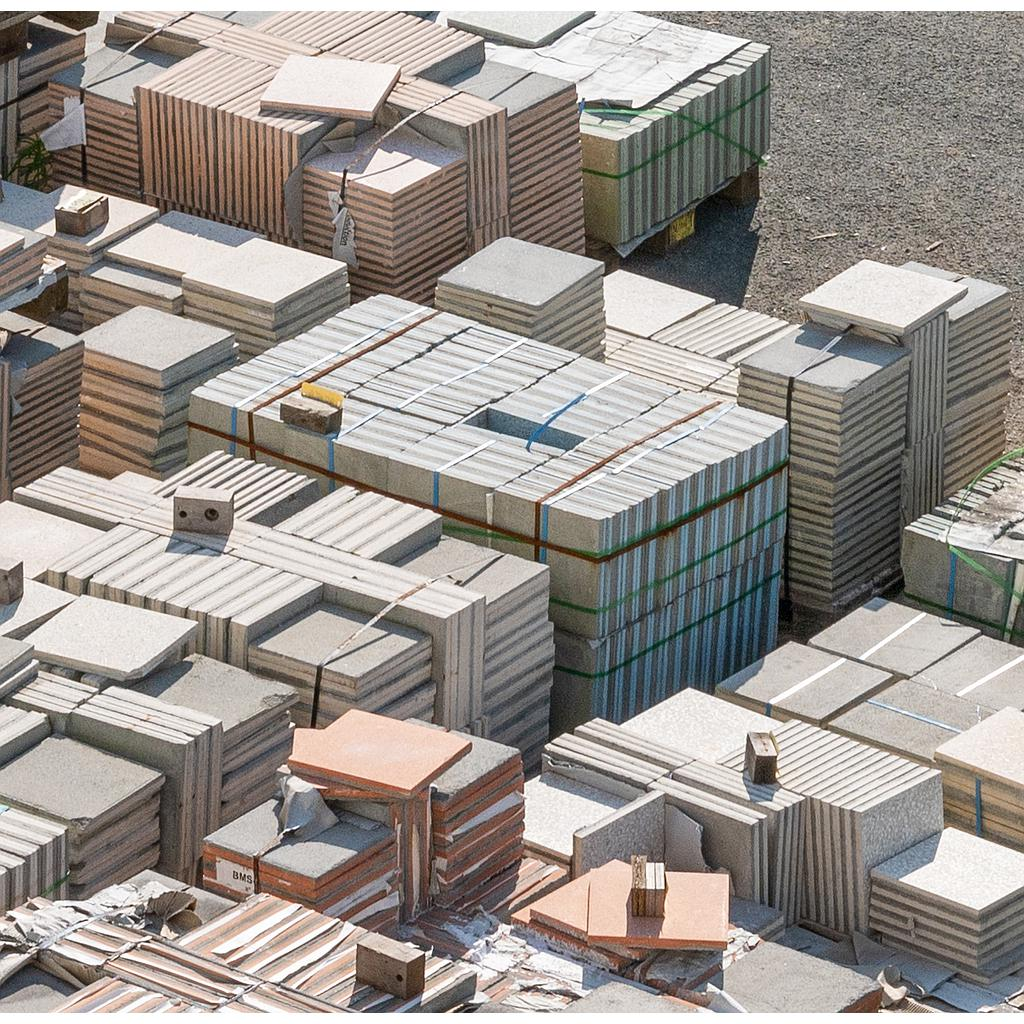
Let’s be clear: shifting to a circular model isn’t without its challenges. It requires upfront design thinking, changes in regulations, and a robust logistics network to manage recovered materials. But the payoff is enormous. Reduced environmental impact, lower material costs, new business models, and buildings that are no longer environmental liabilities but future material banks.
As cities grow and resources become scarcer, the circular economy offers not just a solution, but a thrilling opportunity to reimagine our built environment. Next time you pass a construction site, imagine the possibilities. Could those bricks become part of a new school? Could that steel beam support a future community center? In the new age of circular construction, the answer is a resounding yes.
It’s time to stop in our tracks and rethink what’s possible. From trash to treasure, the future of construction is not only about building—but about rebuilding, reusing, and reinvigorating our world, one salvaged beam at a time.