Inside A.V. Birch: A Interview with Graham Clark on Driving Innovation and Leading the Future of Timber Engineering
A.V. Birch, based in Shropshire, England, has long been a leader in the design and manufacture of industrial automation and timber engineering solutions. Founded in 1977, the company has built a strong reputation for its expertise in mechanical handling, bespoke automation, and bespoke machinery design, serving industries ranging from automotive to aerospace but with its main focus being Timber Engineering. With over five decades of experience, A.V. Birch continues to innovate, pushing the boundaries of what’s possible in industrial engineering by offering customized solutions that meet the unique demands of each client.
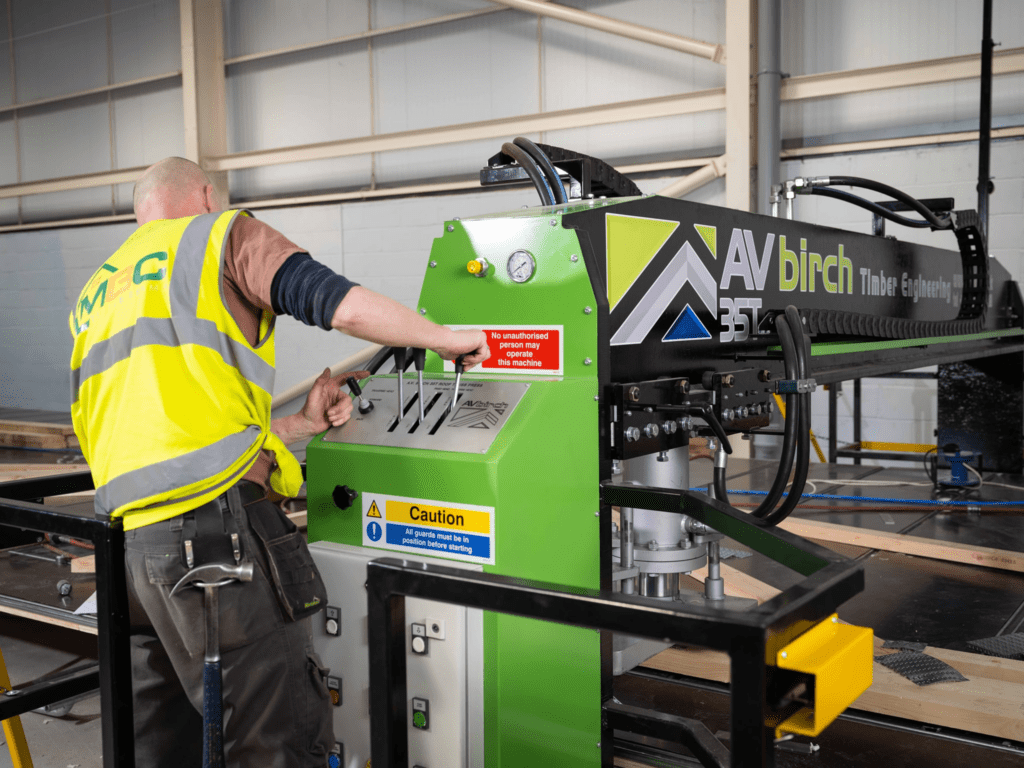
At the heart of A.V. Birch’s continued success is a fantastic team, whose vision has guided the company through both industry challenges and technological advancements. Known for their forward-thinking approach, they have been instrumental in expanding the company’s portfolio and fostering a culture of innovation within the business.
The team at A.V. Birch has maintained its competitive edge in an ever-evolving market while staying true to the core principles of quality and reliability that have defined the company since its inception.
In this exclusive interview, we sit down with one of A.V. Birch’s owners to discuss the company’s journey, its commitment to engineering excellence, and the future of industrial automation. We explore the pivotal decisions that have shaped the business and gain insight into the strategic vision that continues to drive A.V. Birch toward future growth and innovation.
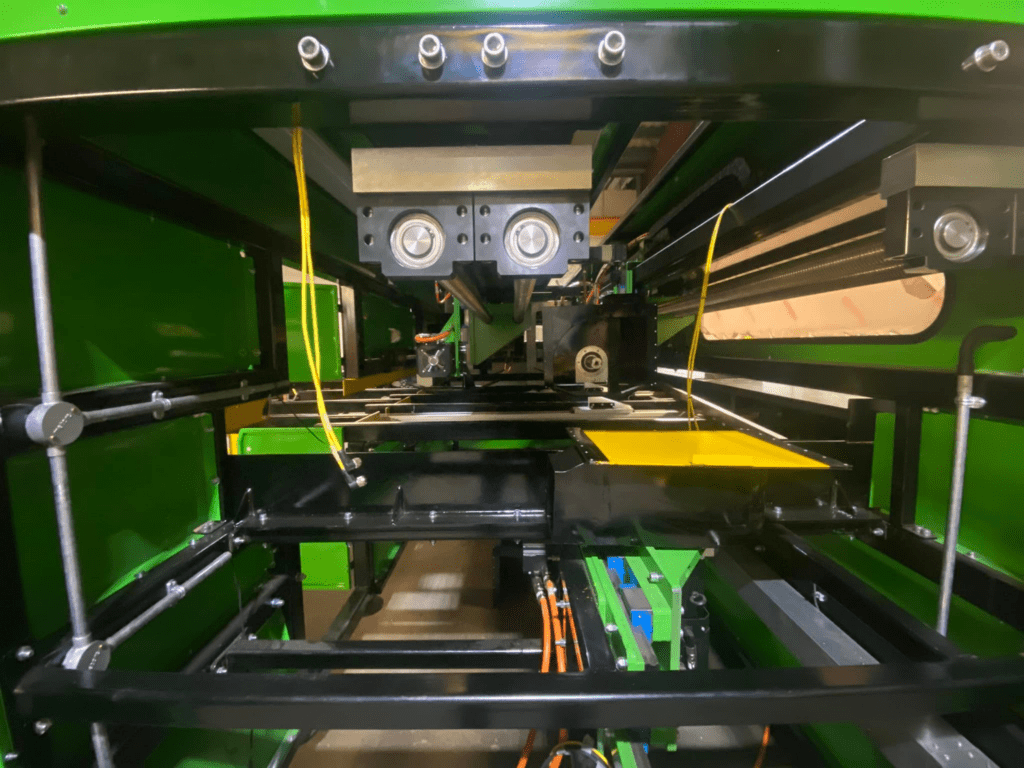
all photos – AV Birch Limited
Gary Fleisher, Offsite Innovators: A.V. Birch has a long history of creating bespoke engineering solutions. How do you foster an innovative culture within the company to ensure it stays at the forefront of industrial automation?
Graham Clark, A.V. Birch: The message is simple, don’t be afraid to think outside of the box, we have designed many bespoke machines using this principle, innovation is key to our business and what keeps us ahead of the competition, our team consists of skills that would guide us through the whole process of designing a machine, it’s not always the latest components we use that may give us that edge but sometimes things like how easily it can be maintained and serviced is something that always gets our attention, this is where having a variety of skill levels in the team can really come Into play.
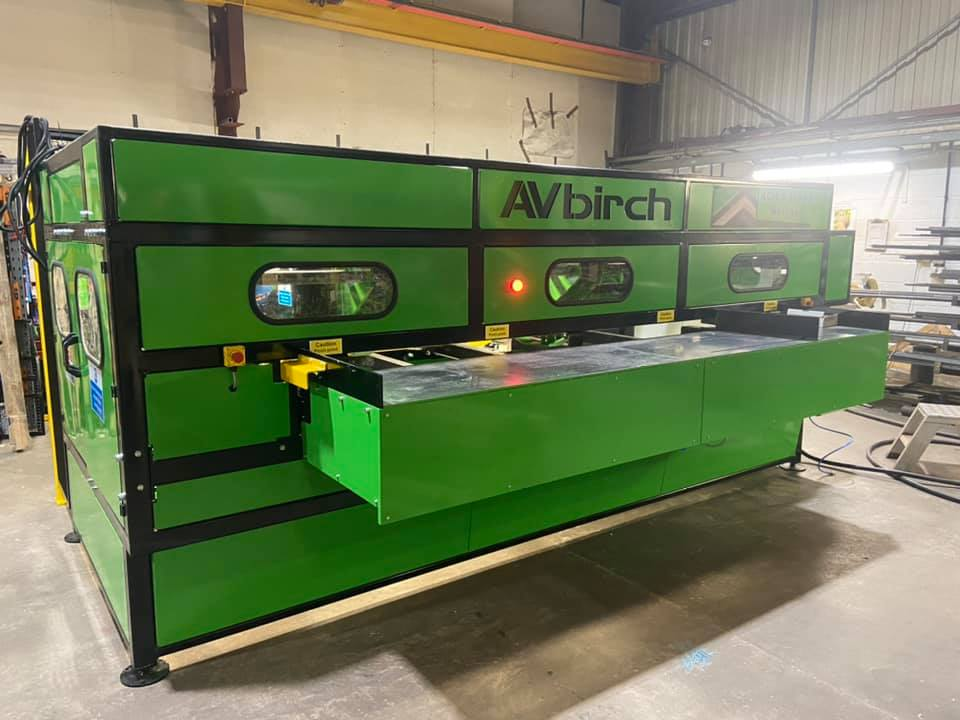
.
Gary: Can you share a recent project where A.V. Birch introduced a groundbreaking solution? What was the driving force behind the innovation, and how did it impact the client’s operations?
Graham: We recently designed and built a machine for creating V notches in wooden fence posts to accept an arris rail, Historically this secondary process has been achieved by using a variety of old antiquated machinery and sometimes even cross-cut saws to achieve the V notch, We started by looking at the existing machinery available and could see that safety and speed were areas that needed some serious thought, also the age of the existing equipment in the industry meant that parts were becoming increasing difficult to get hold of so maintenance/downtime was also an issue, these became the primary targets for design.
The next stage was to come up with a way of cutting the V notch efficiently and safely, again thinking outside of the box we looked at CNC machines that were used in different industries and soon came to the conclusion that a specially designed rotary cutting tool would give us this, we also found that unlike the existing saws and chisel type machines using a cutting tool like this gave us priceless feedback to its longevity as we were able to study the data fed back to us from the loads on the motors during the cutting process so the design of the control and tooling was focused around this.
Speed and efficiency are always very important to any customer, and we looked at the current numbers supplied by the customer who was using a mix of saw and chisel machines to create the V notch, their existing process would involve many members of staff and countless hours, we were told that to cut a pack of timber posts would take them on average 2 hrs., so in essence the target was set.
Designed then progressed and we were very happy to deliver a machine that is the first of its kind, possibly the most important aspect for a business owner sometimes is as simple as “how fast is it “ well our machine is fast, if you compare cutting times alone we have gone from the existing process taking 2hrs to our machine delivering the same numbers in 7-15minutes. Not only did it deliver impressive production figures but perhaps more importantly we delivered a machine that was safe and met current regulations, parts were easily accessible, the quality of cut was far superior and the machine required half of the labor to operate.

.
Gary: With technology evolving rapidly, how does A.V. Birch integrate emerging technologies, such as automation and digital solutions, into its core services while maintaining the company’s longstanding values?
Graham: We have been in the business long enough to see how machinery has evolved and we have played a large part in delivering safe efficient machinery to the truss and floor joist world of timber engineering, it’s easy to see that modern technology can make a huge difference in certain applications, but not all, it’s having the knowledge to know when and how to use it. This takes a team time to break down the requirements of each inquiry and to understand what the customer actually requires and it is sometimes not what they think, there seems to be a misconception that robotics for example are the future, yes in some circumstances they are, however when looking at some applications it doesn’t stack up.
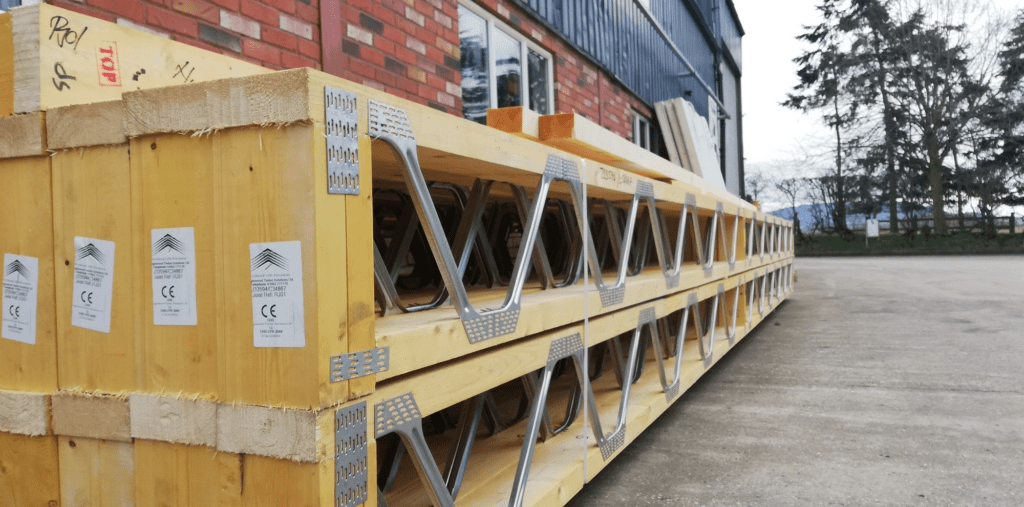
.
Gary: What role do customer needs and feedback play in shaping the direction of A.V. Birch’s innovation strategy, and how does the company stay agile in responding to changing industry demands?
Graham: The customers’ needs are undeniably what drives us, delivering more is always the objective. Without forward-thinking businesses, we wouldn’t be designing new machinery. It generally starts with a conversation about inefficiencies or difficult time-consuming processes that don’t have a solution, could you tell me this is something we often hear, how we then go about solving this is the real heartbeat of everything we stand for.
Gary: As a leader in timber engineering equipment, what are some of the key trends you see in the industry today, and how is A.V. Birch positioning itself to capitalize on these trends through innovation?
Graham: The key trends aren’t necessarily any different from what they always have been, the strive for innovation, efficiency, productivity, and safety is at the top of any manufacturer’s agenda, we like to think that we have positioned ourselves to be the supplier of the best machinery, we have a reputation for building bomb-proof equipment with a focus on easily maintainable equipment that lasts, we have truss presses that are still producing trusses 30-40 years down the line. Having said that, continual innovation is the key and we are always looking at how we can improve efficiencies.
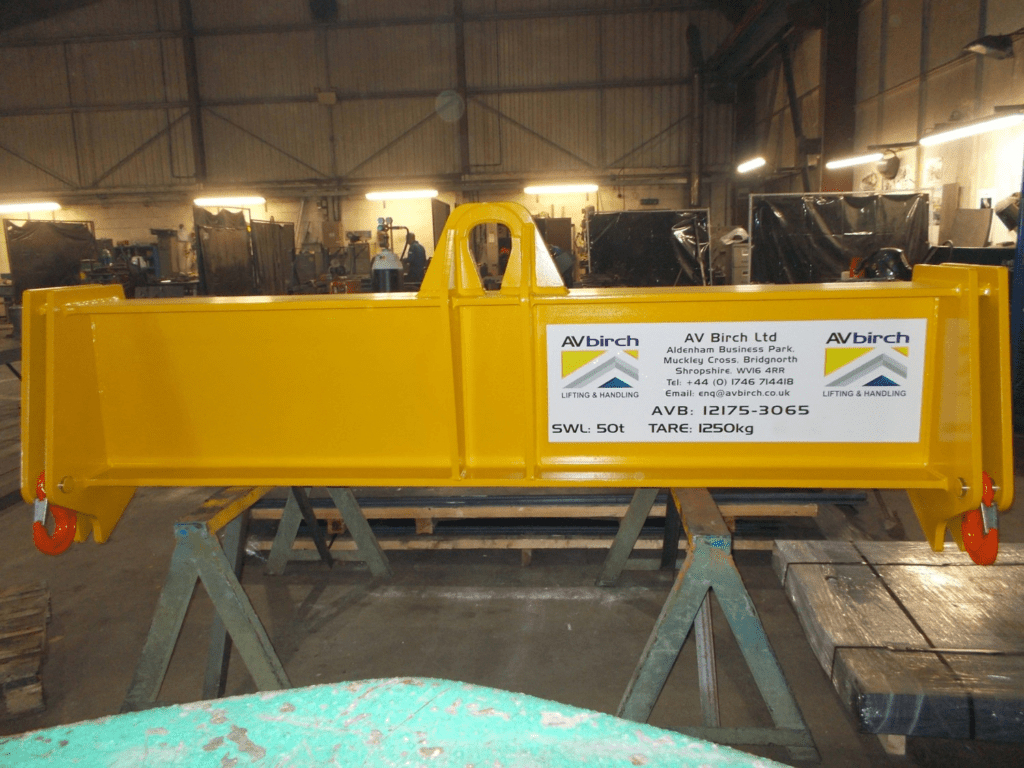
Here’s one of our 50T lifting beams. They’re designed for picking up large steel coils that weigh up to 50 tons. The hooks are rated at 20T each.
Gary: Looking ahead, what are your priorities for A.V. Birch in terms of future innovation? Are there any emerging markets or technologies that you believe will significantly shape the company’s direction in the coming years?
Graham: Looking ahead it is to stay at the forefront of Timber engineering equipment, the emerging markets in MMC show a willingness to move with the times, we have all seen the benefits of this type of construction within the UK already and we are there to support with machinery, our latest Truss Auto Press sits nicely between others in the market giving options to customers depending on their preference and budget which is important, We have also witnessed the growth in metal webs for floor joists, our uni-roll is the best selling machine in the market.
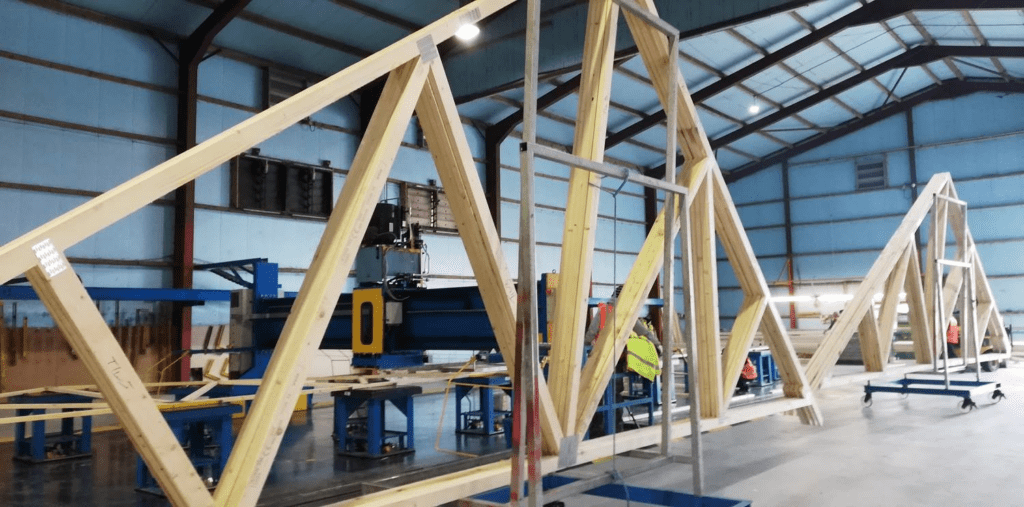
.
I want to thank Graham and the wonderful team for allowing us to look behind the curtain at one of the world’s best-run and innovative timber engineering equipment companies.
.