An Amazing In-Depth Interview with Thunderhaus Innovator – Paul Richards
Paul Richards, a dynamic leader and innovator in the offsite construction industry, is
making waves with his latest venture, The Thunderhaus site production system. Known
for his forward-thinking approach and extensive experience in construction, Paul is
pushing boundaries once again with these innovative systems designed to streamline
and enhance the efficiency of building processes in even the most challenging
Environments.
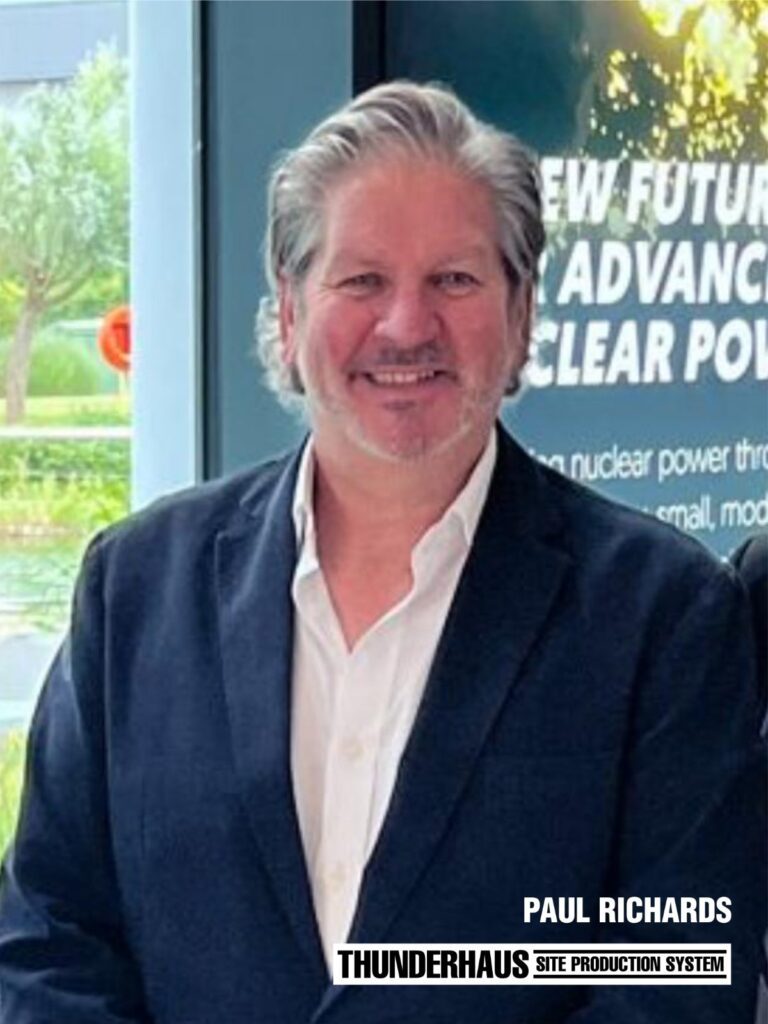
With 40 years of experience in construction, Paul Richards has a multidisciplinary
background that spans 20 years as a factory owner/operator, specializing in DFMA
and delivering thousands of projects. In parallel, he self-financed an R&D facility for
over a decade focusing on ballistic composites for retrofits/newbuild, designing &
building machinery and developing processes for mass production, training
manufacturers globally, and integrating robotic production systems. His advisory roles
include contributions to the UK Government’s Construction Innovation Hub and various
European retrofit/newbuild sustainability programs. Paul is also the developer of the
Thunderhaus site production system, a cutting-edge innovation aimed at improving
onsite life while delivering efficiency and building truly affordable energy energy-efficient
Housing.
I interviewed Paul to learn more about him and his innovative Thunderhaus concept, exploring its impact, potential, and
what it means for the future of offsite construction.

.
Gary Fleisher, cofounder of OffsiteInnovators: What was the initial inspiration behind the Thunderhaus site production system,
and how did it evolve from concept to reality?
Paul Richards, Thunderhaus innovator: well it started out like most innovations as a solution to a simple problem, I can
trace my early attempts back to the 90’s when one of my guys approached me during a
long wet winter, and a very wet start to the new year, they’d had enough, he opened up
to me and I knew I needed to act, so I bult a cover to protect a site and I thought that
could give them a good few weeks dry work, and try to kick start the year, it worked well,
sort of , yeah not perfect but it worked, and then the storms came and it didn’t! but that
was the spark, and the idea was brewing, but I sold that business and left the onsite
world, or at least I thought I had. Only to return years later having worked around the
globe and seeing how everyone else was building, and adopting new methods, but I
thought this would never be allowed in the UK or Would it? And unfortunately for me
that was the start of everything.
But guess what it still rains here in the UK and people can’t work! How dumb, no other
industry would work like this, its time for a shake up!
The penny was starting to drop during my Retrofit for the Future investigations our
Government held a £150million program to retrofit the Uk’s existing housing stock, they
stripped back various existing houses and re built them with every emerging technology
to bring these homes into the future, but I could see a pattern running throughout these
100 test houses, and I could see what was lacking, so again this was only fueling my
Thoughts.
Years later I heard Mark Farmer speak, and it was as if I wrote his message, Modernize
or Die! I heard that and filled in the Blanks, this was it for me, he was effectively saying,
we the industry needed to adopt new technology and solutions within the Built
environment “well that’s what I was hearing” this was my time. I had a housing system in
my head that was formed when I was a teenager on commercial sites, and would be
building huge commercial buildings across the UK while my mates were rolling around
back at home in the mud, still trying to place a brick on a brick in the Rain, my wealthy
friends would pay good money to watch mud wrestling with beautiful ladies showing
their underwear while wrestling with each other in the mud, well you could see this
every day onsite in the winter for free, except the beautiful, and the ladies, but the guys
were as covered in mud, and you could see their underwear, so not so different. But that
type of work wasn’t for me and its certainly not for the youngsters of today. So, another
reason for change. Over the next few years, I had perfected the housing system and
developed it into a Kit of parts, but industry wasn’t interested. They were interested in
large scale factory production, factory built homes were being hailed as the panacea for
the industry hailed by everyone who has probably never paid to set up or operate a
factory for the construction industry out of their own pocket, but I have, when I opened
my first facility, in my early 20,s, I grew my business and needed a bigger factory, and a
bigger one, and a bigger one, you get the picture, but maintaining that model is costly, in
every way imaginable, I used to work “silly o’clock” I’ve always done it 7 days a week,
silly o’clock, but my team was getting fed up, we didn’t know what day of the week it
was, we were just working and working, but I was young and naive.
Again, one of my team approached me and said, “we had to change”! He was right, so
we reached out to the supply chain and I started engaging with effectively my
competition, and it worked, they started to make our components, “subassemblies”
eventually we stopped working 7 days and started taking weekends off, ok they did, it
took a while for me, but the atmosphere was much better, and I started developing ways
to communicate with my supply chain, there were no computers back then that we knew
how to use, and my supply chain were at different levels of understanding technology,
“Sounding familiar”!! so that could lead to costly mistakes.
But our business continued to grow, and we invested in technology, and working with
the supply chain, which freed me up, and it didn’t need me so much, and as we refined
our models, we didn’t need large Factories, so that enabled me to start on a idea I had,
and I started my first R&D facility. I ran that in Parelle with my other business, I learned
so much not all of it good, but that’s crucial to this journey.
I went on to set up other manufacturing facilities one in Wales and a production line in
Canada, so my understanding of factory needs and more importantly, don’t need, come
from lived experiences, and how to simplify how we communicated.
Back to the Thunderhaus, I know I have simplified the system, (the kit of parts), and that
opens the market, for anyone to engage, mixed that with digital technologies making
understanding sharing correct information easier and people start to get interested.
So, do I need a factory? that word “Need” would define my understanding of every
aspect of what “Needs” to happen, and “defining those Needs” are Key to solid fact-
finding solutions.
So, I have a system that can build Homes, now I had to validate it! And inform industry,
I grew up in a cold house! It was a solid structure but cold in winter, during my time in
Vancouver my friends were building a home after they had just sold their business to
Mrs “G”, so money wasn’t a problem. it was December and cold outside, as I walked
into the house it was warm, I asked the builder how you are heating this place? he said
they weren’t! a house at the same stage of construction in the UK would be a very cold
environment and unpleasant working conditions but this was a bright and warm place to
work, and I discovered how! That was my first real experience of Passive Haus
principles. And I was hooked! Eventually this would influence my system, although the
term Passive hadn’t been termed until a few years later, but I just had to design my
system to PHP by default, But I also knew industry won’t pay extra for this, so I
designed the products with the supply chain to enable this by default. That took a while,
but during that time I went out to the market to shout about it, just when they had
announced they were investing hundreds of millions in Volumetric factory production,
and didn’t understand passive Haus or a kit of parts approach, that simply went against
the Grain of their factory investments.
But I carried on and woke up a land broker that had several sites on stop due to funding
constraints and started to bring him up to speed with offsite technology, but we would
need a factory he said, and I pitched The Thunderhaus, he arranged meetings with
bigger and bigger land brokers which lead me to the big table, ok it wasn’t so big, but
the people were or rather the money they represented was. By then the mega Factory
keys had started to lose their luster, and I found myself sat at the table of plenty, and
they had an idea of what I was trying to address with my Thunderhaus, I can’t say that
they were the people behind the funding of the Largest volumetric factory here in the
UK, I’ll leave that for someone else, but they knew something was amiss with large
factory production and they were sat with me.
“The Carrot and the Thunderhaus” I had several meetings driving up to Manchester
from Bristol we met at the same place, and the Carrot was dropped “booom.“ the
People sat at that table represented big money/ in fact the biggest carrot I’ve heard to
date. One had a fund of £12Billion, yeah with a “B” the other had a fund of £28Billion,
yeah BBBB BBB, but they were still stuck with a fixed factory mindset, they wanted to
do the same thing as before but with a different outcome? I thought. I was going
backwards, tell me about your Factory idea! so I did, “The Thunderhaus”, and I went on
to describe its functions, but it sounded to simplistic to be a viable investment they
weren’t getting it. Nor was I really trying to sell it, But I was asked to find a large factory
in the North for me to set up and operate and they saw this as a business model they
could understand, and a starting place to develop the Thunderhaus, but that wasn’t for
me, I had to decline, as my gut wasn’t happy, and I’ve ignored it in the past to my regret,
Yeah, I had to walk away it took a few days to sink in, because of what I was walking
away from, but I’ve had factories and fixed Factories aren’t for me any more, and once
you start them you can’t just change direction. Oh, and I lied about the Days it still
haunts me now years later because I knew these guys were real and so was their
Money.
But when I was describing the Thunderhaus they mentioned their sites were in
Manchester and my idea of the “super tent” as it was then, wasn’t going to prevent
some scallywags from looting the place, so right there I had the idea of steel structurers
as opposed to an all-fabric building. And the dots started connecting, endless
possibilities.
I haven’t gone back to that table but those sorts of funds seem to pop up along the way
so who knows.
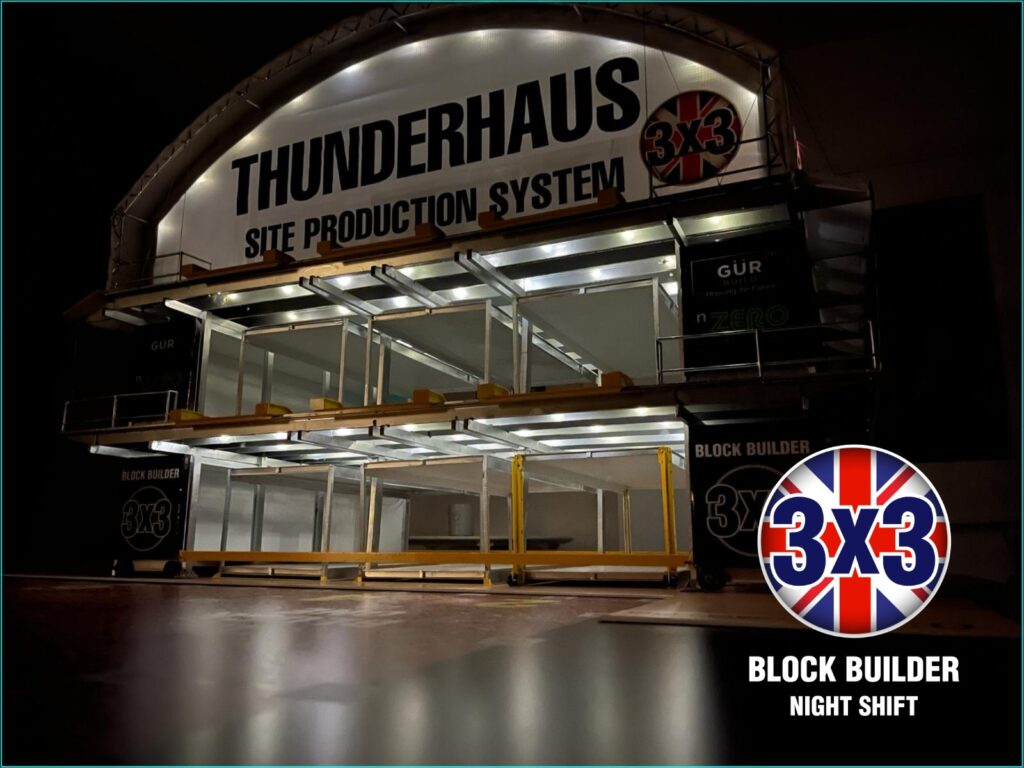
.
Gary: Thunderhaus is designed to work efficiently in challenging conditions, such as
night-time and wintertime. Can you elaborate on the key features that enable this
adaptability?
Paul: Yes, you treat this the same as a fixed factory, but its on site, all the factory kit but
on site. I say if the teams can get to site then they should be able to work protected from
the elements, I’ve worked in Canada and the US and yeah the snow can stop people
getting to site, or even stop work all together, but when I was a kid I got to work by hook
or by crook, but I got there, but the Thunderhaus is effectively a big cover that keeps the
teams dry and warm and protects the build and materials, but that’s the very basic
function of the Thunderhaus, It started out as a building Rig to hold and position
components precisely while they are being assembled, I wanted to de skill this or de risk
the build, using the Rig as the quality and precision enabler by default, I wanted non
skilled people to engage with Housebuilding, ok women, they will make fantastic house
builders, and by using a building Rig with a cover over it derisks the assembly and
enables them to work better than most blokes, I’ve seen it work before and this is the
opportunity for them to thrive. Factory production techniques, we teach people to
specialize is efficiencies, and we advance our subassemblies to enable this, and
develop the support tooling to enable this, but like no other housing site we can
introduce a 3 shift working system, or a much more flexible working environment, that
enable family life to continue while the parents work, I’ve even designed a creche
Thunderhaus, and that will transform the housing industry forever. But it must be
implemented at the earliest stage, it’s a site production system, and everything must be
designed to maximize efficiency of onsite production, and that’s not easy, usually I get
called in when the housing has been designed and the plans been approved but funding
is asking more from the site. This isn’t ideal for the Thunderhaus, although its not
impossible, as I have tried to introduce the Thunderhaus but the benefits were not
enough seeing as they already had a factory and don’t care if everyone and every thing
gets soaked, but that’s changing the teams can still get wet, they aren’t worried about
them, but the warrantee providers are changing the way, if the product isn’t protected
throughout the build stage, they wont be warrantying it, and that applies to Timber
structures more than most.so protecting your product & building in a controlled
environment and making use of factory processes and procedures , what’s not to like?
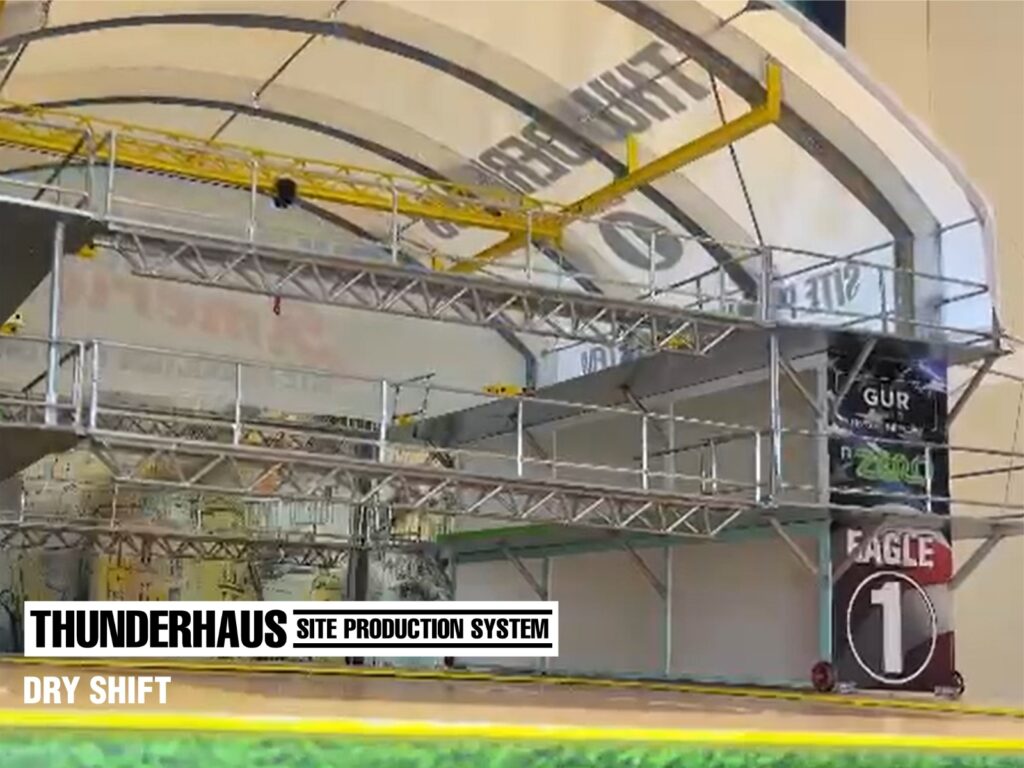
.
Gary: How do you see Thunderhaus impacting the current workflow of site production,
particularly in terms of speed, cost efficiency, and labor demands?
Paul: The Thunderhaus is a production enabler, how many times have people
doublehanded product, built the right thing but in the wrong place, materials damaged or
unfinished or uncompleted tasks lied about the stages of build and that only misinforms
the next trade of their ability to complete their job, this has been the norm for decades
on site, and thousands are lost through in efficiencies. but the Thunderhaus can work
with the builder as a support mechanism, breaking down the tasks and aiding building
efficiencies, it can have & hold parts or tools, but that’s just the basics, decent lighting
and power creating a warm environment and even serve the coffee, this is about
working smarter not harder, let the Rig carry the load, and introduce production
mindsets not builder, pay better because of efficient build processes and advance
subassemblies that can be replicated throughout all your developments, but the
Thunderhaus will prove it worth and will be used In may forms, from subassembly 1
through to multiple riggs traversing on site.
The Thunderhaus will attract the best tradespeople as well as non-trades as builders
are looking to work in a better safer environment and not kill themselves doing so, it will
also open the opportunity for older trades to come back on site in a more respectful
environment,

.
Gary: One of your recent posts mentioned that Thunderhaus is a “catalyst product.” Can you explain what makes it a catalyst and how it could potentially disrupt traditional site
production methods?
Paul: Oh, this is a big one, over the last 5- 10yrs industry has really ramped up its
efforts to push innovations, but they are Siloed, usually great ideas but disconnected
from the real opportunity, where are they going to come together? and certainly not
accessible or visible to the masses, so take up will de prolonged due to the mindset of
the builder, their no nonsense approach to technology has to be taken into
consideration, they need to try it kick the Tires, and see the benefits in their pockets,
before they will believe the hype. So how can this be addressed? Where can they see
these new advancements being used, and what environment will it need to work
effectively, The Thunderhaus is a hosting system, an onsite environment that enable
Man and Machine to work in a controlled environment, it protects the delicate machinery
from the elements , but enables known innovations to actively work on construction
sites, “BOTDEX” is a site floor matting system, this simple floor mat used by the Military
and festival industry simply creates ground surfaces that enable clean floors suitable for
heavy kit to move onsite without difficulty, this simple solution opens up the possibility to
use off the shelf Robotic carriers that are common place in large warehouse activity, it
also enables the Thunderhaus to work 360 degrees, as the need for set tracks have
been eliminated, BOTDEX can do much more than this, it can assist with setting out as
its perfectly square and can be marked at fixed build positions, again connecting
technologies, the gantry systems can be hydraulically controlled, so setting heights and
projections can be altered to support comfortable build heights and prevent
overreaching, the gantry’s at different levels can be accessed by external lifts never
utilized in housebuilding, this could enable wheelchair access and open up untapped
people to work on site. The main bodies of the Thunderhaus can be kitted out for
manufacturing or as office space, The working body of the Thunderhaus can be fitted
out for bespoke requirements with internal gantry cranes for lifting and positioning, we
can set cameras into the frame of the Thunderhaus for safety and monitoring, but I
believe the Real innovation will be a live feed enabler, opening up the possibility to track
build schedules without having to visit the site, and this opens up JIT production linked
to digital ordering but the new opportunity will be the ability to open up new funding
mechanisms, this real time quantifier will enable new funders that invest at set stages,
smaller funders similar to Crowd funding, opening up Housebuilding like never before.
All because of The Thunderhaus.
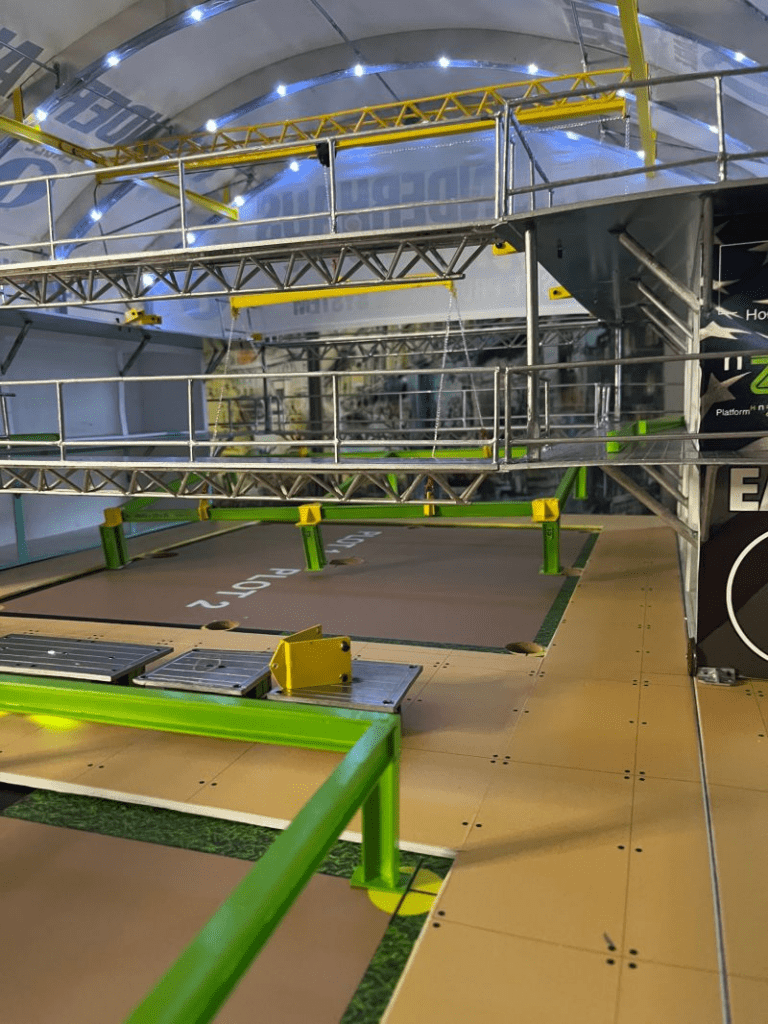
.
Gary: Given the rapid advancements in offsite and modular construction, what role do
you envision Thunderhaus playing in the future of the industry, especially in terms of
scalability and sustainability?
Paul: so I’ve been asked to design different models of the Thunderhaus, and the Block
Builder is based of a Volumetric assembler and install, it’s a little bit Fantastical for some
but the Guts of the idea are there, but the real value is it’s a cheap factory its yours
kitted out how you want it but more importantly its where you need it, fixed factories can
be hundreds of miles for the build site and this enables everything to go wrong, if it can
it will, but the Thunderhaus can be on site or near site, or both, its not limited, and the
best part , when your finished with it you can pack it away and take it to your next site
and start again, I believe the Thunderhaus will be a rental option with the component’s
being generalized, this will enable proven systems that have been perfected by the
industry to be used across the Globe, and simply installed on the build site following a
set sequence laid out by the Thunderhaus. Or “Thousands of Thunderhaus”!
Gary: What were some of the biggest challenges you are facing in the development of
Thunderhaus, and how are you overcoming them to bring this innovation to market?
Paul: well, they still are, The Thunderhaus seems too easy, why hasn’t it been done
before? And then people try and find reasons why it won’t work, they don’t like change,
but that’s nothing New, however, something must change! The need for housing is
greater than ever before, and without trying we aren’t going to know! I can find lots of
reasons why it won’t work, but thousands of reasons why it will, I’ve been around the
Block and construction particularly house building doesn’t appeal to the new generation
of workers and site Life has to change, there are Thousands of young people that will
absolutely thrive onsite and make a fantastic life for them and the people who the Build
for, but they are not thinking construction as their first choice Why? Because getting wet
cold and treated like shit isn’t for them, and its not for me it never has been and it never
will, we need to Respect our young and especially our future trades people, without
them our housing stock will perish and so will our economies, for too long has the
Housing industry been left to stew in a mess created by non-industry pressures and that
has to change. And I believe the Thunderhaus is a great start. But Who’s interested
who’s listening who understands where to start?
Gary: Looking ahead, what future enhancements or additions do you have planned for
the Thunderhaus system, and how do you plan to keep it at the forefront of site
production technology?
Paul: Absolutely, I’ve started the imagination of some very clever people, and they are
onboard, very senior engineers that took a while to get it, have got it, and they are
joining the dots, I’ve been fortunate to work with some clever people, and that’s what
gets me through the negative meetings, these people get it, they know it’s a Catalyst
system in every sense, what the construction industry doesn’t know is these teams have
been looking for solutions for decades but you can have a clever factory somewhere
producing magic, but the magic needs to be seen, and I think the Thunderhaus will be
bringing the magic to your site! Just needs you to be on the stage.
Gary like most innovations we will never know where it will end up or evolve, the World
is full of smarter people than me and I cant wait to see what they can do with the
Thunderhaus!
Gary: I can’t believe all the work and thought you’ve put into this innovative project and want to thank you for a great interview.